MAT stellt die Weichen für eine digitale Zukunft
von Angelika Albrecht
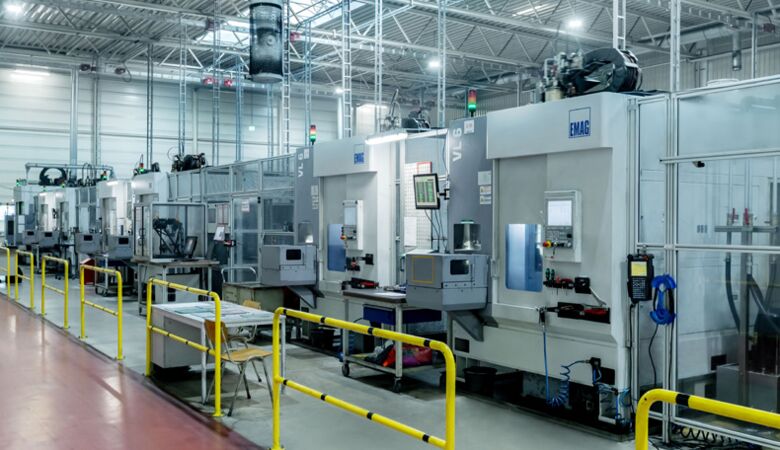
Für viele Produktionsplaner ist die „Industrie 4.0“ ein visionärer Leitgedanke: Maschinen bilden ein ganzheitliches System, das Produktionsplaner von zentraler Stelle überwachen, steuern und auswerten. Dass ein solcher Ansatz keine Zukunftsmusik mehr ist, zeigt eine beeindruckende Produktionslösung bei der MAT Machining Europe GmbH mit Sitz in Immenhausen. Das Automotive-Zulieferunternehmen fertigt komplexe Ausgleichsgetriebegehäuse auf vollautomatisierten EMAG Produktionslinien – und das inklusive einer weitreichenden Datenerfassung und –auswertung von Maschinendaten.
Die Zielsetzung dabei ist: Die Ausbringung der Linien soll signifikant ansteigen und die Prozesssicherheit deutlich verbessert werden. Das Gesamtsystem ist bereits fest im Arbeitsablauf implementiert.
Der Produktionsprozess bei der MAT Machining Europe GmbH rund um das Ausgleichsgetriebegehäuse ist beeindruckend: Das Unternehmen verfügt insgesamt über fünf große Produktionslinien mit jeweils sieben EMAG Maschinen, die per TrackMotion von EMAG verkettet sind. Dabei fährt eine sogenannte TransLift-Einheit auf einem Schienensystem „durch“ die Maschinen und transportiert das Bauteil von einer Pick-Up-Station zur nächsten. Auf diese Weise vollziehen sich am Getriebegehäuse diverse Vorprozesse, das Drehen der ersten Seite inklusive der Bearbeitung von Passungen und Bohrungen, das Drehen der zweiten Seite und der Außenkontur sowie – in der letzten Ausspannung – die Innenbearbeitung von Kugelform und Passbohrungen. Zum Abschluss folgen Waschen, Messen und Markieren. Insgesamt entstehen fast 2 Millionen Ausgleichsgetriebegehäuse bei MAT pro Jahr alleine am Standort Immenhausen.
Win-Win-Situation ausnutzen
„Wir setzen allgemein auf hocheffiziente State-of-the-art-Produktionslösungen, die wir laufend weiterentwickeln. Die Digitalisierung ist dabei natürlich ein wichtiges Thema“, sagt dazu Axel Dräger, Leiter Engineering bei der MAT Machining Europe GmbH. „Wir wussten auch, dass EMAG in den letzten Jahren große Anstrengungen rund um die Industrie 4.0 unternommen hat und ganz grundsätzlich daran interessiert ist, neue IoT-Lösungen bei Anwendern zu testen und ein qualifiziertes Feedback zu bekommen. Für beide Unternehmen ist das Ganze also eine Win-Win-Situation.“
Das Projekt startete im Frühjahr 2019 zunächst mit Workshops: MAT-Verantwortliche stellten den IoT-Experten von EMAG sowie den Partner-Unternehmen EXXETA, intuity und anacision die Produktionsprozesse rund um das Ausgleichsgetriebegehäuse vor. Wichtig war in diesem Zusammenhang, dass die Lösung von EMAG eine vollkommen modulare Software- und Hardware-Architektur aufweist, die sich einfach in die IT-Infrastrukturen der Anwender und die meisten EMAG Maschinen (auch älteren Typs) implementieren lässt. Der Anschluss von zusätzlicher Sensorik stellt ebenso kein Problem dar.
Ausbringung deutlich steigern – Prozesssicherheit verbessern
Die Handhabung der Daten durch Anwender erfolgt wiederum mithilfe des EDNA Lifeline Dashboards, auf dem die angesprochenen Apps für verschiedene Anwendungen installiert sind – der Anwender kann sich selbst zusammenstellen, was genau in welcher Anordnung zu sehen ist.
„Insgesamt ist die Datenmenge tatsächlich so vielfältig, dass wir bislang nur einen Teil analysieren“, erklärt Dräger. „Nichtsdestotrotz sind die ersten Ergebnisse beeindruckend. Wir haben beispielsweise bereits diverse ‚Zeitfresser‘ eliminiert und sind auf dem besten Weg zu einer Ausbringungssteigerung von elf Prozent. Das ist natürlich ein enormer Wert.“
Außerdem profitieren die Spezialisten bei MAT von der laufenden sensorischen Überwachung: Das System ermittelt einen präzisen „Gesundheitswert“ von Antrieb sowie Spindel und weist auf etwaigen Verschleiß frühzeitig hin – ein großer Pluspunkt für die Prozesssicherheit der Produktionslinien. Gleiches gilt für die präzise Vorhersage des richtigen Zeitpunkts bei Werkzeugwechseln.
Darüber hinaus ist das EDNA-System fest im Arbeitsablauf von MAT implementiert: Einerseits nutzen Produktionsplaner oder Schichtführer die Dashboards, um aktuell produzierte Stückzahlen zu ermitteln. Andererseits können Bediener ihren Arbeitsablauf mithilfe der Software besser planen, weil sie nach einer Pause rechtzeitig an der Maschine zurück sind oder bei einem anstehenden Werkzeugtausch immer die „richtigen“ Tools bereit liegen.
MAT stellt die Weichen für eine digitale Zukunft.
„Viele sprechen darüber, wir bauen gerade die digitale Fabrik,“ erklärt der verantwortliche Geschäftsführer der MAT Transmission Division und CEO der MAT Europe, Ingo Bitzer.
Weitere Anwendungsfälle im Fokus
Insgesamt betrachten beide Partner das gesamte Projekt keineswegs als abgeschlossen. "Die Digitalisierung der MAT Produktion schreitet mit Hochdruck weiter voran," bestätigt Dr. Andreas Kühne, Lead Data Scientist beim Unternehmen anacision, an dem EMAG beteiligt ist: „Unser gemeinsames Ziel ist es, weitere Linien mit dieser IoT-Lösung auszustatten. Außerdem möchten wir neue Anwendungsfälle wie etwa die Werkzeugbrucherkennung umsetzen. Dazu tauschen wir uns nach wie vor eng aus.“
Alle Vorarbeiten erfolgen bei EMAG, wo das System passgenau für die gewünschte Lösung konfiguriert und für die Anbindung an verschiedene Maschinensteuerungen vorbereitet wird. Nach der Implementierung in den Maschinen vor Ort profitiert der Anwender sehr schnell von den gewünschten Funktionalitäten und Prozessverbesserungen. Anwender profitieren zudem von einem umfassenden, offenen und zukunftssicheren Industie-4.0-Ökosystem. Mit der EDNA Industrie 4.0 Lösung legt EMAG den Grundstein für die intelligente Produktion der Zukunft.
Quelle und Bilder: EMAG GmbH & Co.KG