Hoch beanspruchte Teile wirtschaftlich strahlen
von Hubert Hunscheidt
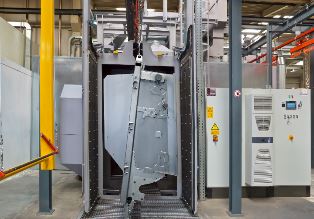
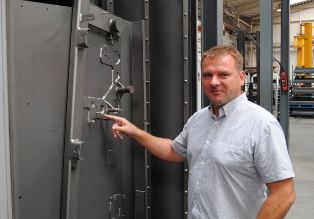
Lifter zum Entleeren von Abfallbehältern und Presseinrichtungen gehören zu den am meisten beanspruchten Teilen an Abfallsammelfahrzeugen. Die andauernde mechanische Handhabung der Tonnen und Container setzt eine gute Lackanhaftung voraus, wenn die Baugruppen lange vor Wettereinflüssen geschützt werden sollen.
„Die Fa. Zoeller Systems spol. s r.o. wurde 1992 als Tochter der deutschen Fa. Zöller - Kipper GmbH, gegründet. Im tschechischen Ort Říčany hat das Unternehmen sein Produktionswerk für Lifter und Presseinrichtungen errichtet“, berichtet CEO Karl-Heinz Wider. „Die Wahl fiel aufgrund der guten verkehrstechnischen Anbindung auf die Region südöstlich von Prag. Außerdem standen gut ausgebildete Fachkräfte zur Verfügung.“
In den letzten 25 Jahren hat sich Zoeller Systems aus kleinen Anfängen zu einem Unternehmen entwickelt, das auf insgesamt 28.000 m² über mehr als 10.000 m² Produktionsfläche verfügt. Die Zahl der Mitarbeiter stieg auf 290 an.
Zu Beginn des Jahres 2018 ist eine neue Oberflächenbehandlungslinie in Betrieb genommen worden. Die Rohteile für Presseinrichtungen und Lifter werden zunächst geschweißt und mechanisch bearbeitet. Die Oberflächenbehandlung erfolgt, nachdem alle fertigungstechnischen Prozesse und Prüfroutinen abgeschlossen sind. „Der Grund für die neue strahltechnische Vorbehandlung der Teile liegt in der Tatsache, dass die Kunden eine hochwertige Oberfläche auch von stark beanspruchten Teilen verlangen“, sagt der Leiter der Lackiererei, Josef Burian. Nun liegen erste Erfahrungen vor.
Die Frage nach dem Grund für die Entscheidung für den Strahlanlagenlieferanten AGTOS beantwortet Burian mit dem überzeugenden Konzept von AGTOS sowie mit der Flexibilität der Anlage. Denn es können große und kleine Teile mit einer gleichbleibenden Qualität bearbeitet werden.
Vor der Anschaffung der neuen Linie wurden verschiedene Untersuchungen vorgenommen, um die beste Vorbehandlung und Beschichtung zu finden. So wurden die mit dem neuen Verfahren beschichteten Oberflächen einem Salzsprühtest unterzogen. Darüber hinaus wurde die Optik der Lifter im Praxiseinsatz mit den Ergebnissen von nach alter Methode beschichteten Werkstücken verglichen. So wurde auch die Geschäftsleitung von der neuen Technologie überzeugt.
Konzept
Vor dem Strahlprozess werden die mechanisch bearbeiteten Bereiche der Werkstücke abgedeckt und damit geschützt. Die Präzision der Bauteile ist maßgehend für die optimale Funktion der Endprodukte.
Die Teile gelangen hängend zur AGTOS Hängebahn-Strahlanlage. Sie werden manuell zugeführt. Schon vor der Strahlkammer ergreift die automatische Einzugsvorrichtung die Schlitten und befördert die Werkstücke einzeln in die Strahlkammer. In Abhängigkeit vom gewählten Strahlprogramm werden sie dort zwischen 3 bis 10 Minuten gestrahlt. Die Werkstücke verlassen die Strahlkammer bestens vorbereitet für die anschließende Nasslackierung.
Die neue Strahlmaschine vom Typ HT 10-20-3.6-08-07,5 verfügt über acht frequenzgesteuerte AGTOS-Hochleistungsturbinen mit je 7,5 KW. Damit gelangt das Strahlmittel auch bei komplexen Geometrien an alle Oberflächen. Nicht nur das Mangangehäuse der Hochleistungsturbinen ist mit leicht auswechselbaren Verschleißplatten aus Werkzeugstahl geschützt. Auch die Strahlkammer selbst wird vor der abrasiven Wirkung des Strahlmittels durch leicht auswechselbare Verschleißplatten aus Mangan-Stahl bestens geschützt.
Das Strahlmittel durchläuft einen Kreislauf. Nach dem Strahlvorgang wird es aufgefangen, gereinigt und dem Prozess dosiert wieder zugeführt. Der beim Strahlvorgang entstehende Staub wird mittels Unterdruck einer Patronenfilteranlage zugeführt und der Luft entzogen. Er wird über einen Big-Bag entsorgt. Ein automatisches Strahlmittelnachfüllsilo sorgt für einen gleichmäßigen Strahlprozess.
Eine Wartungsbühne ermöglicht Wartungs- und Einstellarbeiten. Sie wird über eine Sicherheitsleiter mit Geländer und Fußschutz erreicht.
Die Strahlmaschine kann Werkstücke mit Maßen bis zu 1x2 m (B x H) aufnehmen und bearbeiten. Ein Doppelbecherwerk reduziert die Bauhöhe und ermöglichte damit die Einpassung in die Halle. Besonderes Augenmerk legte der Kunde auf die Staubfreiheit des Prozesses, die durch die effektive AGTOS Patronenfilteranlage sichergestellt wird. Sie ist so ausgelegt, dass die gereinigte Luft in die Halle zurückgeführt werden kann. Dies dient der Energieeffizienz und spart damit Heizkosten.
Eine manuelle Abblassstation ermöglicht es dem Bediener bei Bedarf, in Sacklöchern verbliebenes Strahlmittel manuell zu entfernen. Herabfallendes Strahlmittel wird in einem 8 m langen Trichter aufgefangen und dem Strahlprozess ebenfalls wieder zugeführt. Der Anteil der manuellen Tätigkeiten beschränkt sich damit auf ein Minimum. Dies unterscheidet den neuen Prozess vom vorherigen eklatant. Zuvor wurden große Teile in einem Freistrahlraum komplett manuell gestrahlt, Kleinteile wurden nicht strahltechnisch behandelt.
Ein Fernwartungsmodul ermöglicht den externen Zugang zur Elektronik der Strahlanlage. Es unterstützt und vereinfacht damit die Störungsbehebung.
Bildtext (Vorschaufoto): Die AGTOS Hängebahn-Strahlanlage HT 10-20-3.6-08-07,5 mit einem gestrahlten Werkstück.
Bildtext (Beitragsfoto): „Der Grund für die neue strahltechnische Vorbehandlung der Teile liegt in der Tatsache, dass die Kunden eine hochwertige Oberfläche auch von stark beanspruchten Teilen verlangen“, sagt der Leiter der Lackiererei, Josef Burian. Er steht vor der AGTOS Hängebahn-Strahlanlage HT 10-20-3.6-08-07,5 mit einem gestrahlten Werkstück.
Quelle und Fotos: AGTOS GmbH