Gießpfannen für das Stahlwerk Georgsmarienhütte
von Alfons Woelfing
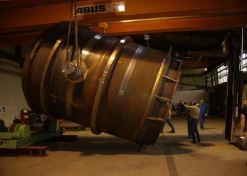
3D-Brennen als Kostenkiller
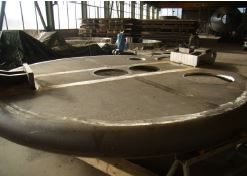
Spiralförmige Stahlrippen in einem Schnitt
Neue Wege ging die Wessel GmbH Kessel- und Apparatebau beim Bau von zwei Gießpfannen für das Stahlwerk Georgsmarienhütte in Osnabrück. Der auf Entwicklung, Bau, Montage und Instandhaltung von Großkesseln spezialisierte Familienbetrieb vertraute auf ein neues Brennschneidverfahren, um teure Fräszeiten bei anspruchsvollen Geometrien zu sparen. Zur Verstärkung der kegelförmigen Pfannengeometrie ließ er 28 leicht spiralförmige Rippen von der Jebens GmbH mit Sitz in Korntal-Münchingen durch 3D-Brennen herstellen. Der führende Spezialist für große schwere Brennteile, mechanische Bearbeitung und komplexe Schweißbaugruppen fertigte mit dem Brennschneidroboter diese Komponenten, deren Winkel sich entlang der gesamten Schnittkante kontinuierlich verändert. Das Ergebnis spricht für sich: Zehn Prozent Kostenersparnis und 25 Prozent Zeitgewinn.
Was vor 40 Jahren in der sprichwörtlichen Garage begann, gilt heute in Deutschland als führende Adresse rund um Engineering, Fertigung, Umbau, Sanierung und Wartung von Großkesseln sowie Großkesselkomponenten. Die 1978 von Manfred Wessel gegründete Firma fertigte zunächst kleinere Druckteilkomponenten. Das Unternehmen wuchs schnell und erweiterte sein Portfolio kontinuierlich. Heute beschäftigt die Wessel GmbH an zwei Standorten in Xanten auf insgesamt 16.000 Quadratmetern Fläche rund 200 Mitarbeiter. Seit 2012 leitet die zweite Generation die Geschicke des Unternehmens. Hauptprodukte sind Kessel und Druckteile für Hütten-, Kraft- und Stahlwerke, Müllverbrennung und Biomasse. Aber auch alle Zusatzaggregate wie Abgasanlagen, Bühnen, Förderer oder Stahlbaugerüste, die den Kessel tragen, fertigt Wessel. Stahlwerksnahe Dienstleistungen zur Nachrüstung, Modernisierung und Instandhaltung bestehender Anlagen runden das Portfolio ab. So setzt beispielsweise die Georgsmarienhütte (GMH) in Osnabrück auf ein 35 Mann starkes Wessel-Team mit eigenem Stützpunkt auf ihrem Gelände. Zweiter großer Geschäftsbereich von Wessel ist die Fördertechnik - nicht nur für Kraft- und Heizwerke, sondern auch für die Futtermittel- und Pellet-Industrie. Modernste technische Anlagen und über Jahrzehnte im Kessel- und Druckbehälterbau gewachsene Ingenieurs- und Schweißkompetenz begründen die führende Rolle des Unternehmens. Beispielhaft für diese Expertise stehen röntgengerechte Schweißnähte, die im Druckbehälterbau eine zwingende Präzisions- und Qualitätsanforderung sind: Bei Wessel sind sie bei nahezu allen Schweißaufgaben etablierter Standard.
Neue Gießpfanne für Stahlwerk
Dieses ausgewiesene Know-how war auch für den Bau von zwei Gießpfannen mit je 150 Tonnen Nutzinhalt für den Schmelzbetrieb im Stahlwerk der GMH gefragt. In ihr wird der flüssige Stahl vom Ofen zur Vakuumbehandlung und weiter zur Stranggussanlage per Kran transportiert. Dabei muss sie Einsatztemperaturen von 1.400°C und Druckwechseln in einer Vakuumanlage ebenso dauerhaft standhalten wie - 3,5 Meter hoch mit flüssigem Stahl befüllt - einem Schweredruck am Boden von bis zu 8 bar. 3,90 Meter hoch, mit einem Durchmesser von fast 3,80 Meter und 30 Millimeter dicker Wandstärke zählt sie zu den großen Pfannenkalibern. Ihr Leergewicht beträgt ohne Mauerwerk 24,5 Tonnen. Mit Mauerwerk und 150 Tonnen Füllung bringt sie 220 Tonnen auf die Waage. Die leicht kegelförmige Pfanne wird mit einem Winkel von 1,3 Grad nach unten hin schmaler - angesichts ihrer Dimension eine entsprechend große Herausforderung für die Passform aller darauf anzubringenden Bauteile.
Den Anfang ihrer Fertigung markierte der Pfannenboden. Er ist - laut Stefan Biniszkiewicz, zuständiger Projektingenieur für Maschinen- und Anlagentechnik bei Wessel und verantwortlicher Projektleiter beim Bau der Gießpfanne - eines der herausforderndsten Bauteile des gesamten Produkts. Bei ihrer Geometrie kann ungleichmäßiges Schweißvolumen leicht zu Verzug führen. Für den Aufbau wurde sie auf große Richtplatten aufgespannt. Anschließend zog Wessel über den konischen Pfannenmantel aus zwei rundgewalzten Mantelschüssen drei massive, bis zu 100 Millimeter dicke nahtlose Verstärkungsringe. Zwei weitere, halbmondförmige Verstärkungsringe gleicher Stärke wurden in Höhe der Tragzapfen angebracht. Zum Ansetzen des Pfannenbodens mit Löchern für Temperaturmesssonde, Abstich und Gasspülung sowie das Schweißen der Rundnähte nutzte Wessel eine eigens für dieses Projekt angepasste Fertigungsvorrichtung mit Rollgang. Dadurch konnten die Kranbewegungen für das 25 Tonnen schwere Endprodukt weitgehend minimiert werden. 18 von Jebens gefertigte Augen mit spezieller Fasengeometrie zur seitlichen Verstärkung des runden Pfannenbodens wurden in dieser Vorrichtung ebenfalls angeschweißt. Nach dem Ansetzen der beiden jeweils 700 Kilogramm schweren, geschmiedeten Tragzapfen wurden die per 3D-Brennen hergestellten Stahlrippen um sie herum sternförmig an dem konusförmigen Pfannenkörper angesetzt. Stück um Stück folgten alle weiteren Anbauteile. Binnen drei Monaten von der Auftragserteilung bis zur Auslieferung an das Stahlwerk war die Gießpfanne fertig. In diesem Zeitraum erzeugten zwölf Schweißer im Dreischichtbetrieb insgesamt fast 550 Kilogramm Schweißnaht: Allein die Rundnaht zwischen Boden und Pfannenbehälter wog 64 Kilogramm. Für die Kundenabnahme ließ Stefan Biniszkiewicz ein 3D-Bild der Pfanne erstellen, das die Abweichung von der idealen Rundheit farblich darstellte. "Der gesamte Pfannenkörper wich nur maximal zwei Millimeter vom Ideal ab - als reiner Stahlbau ohne mechanische Bearbeitung", erzählt er stolz und ergänzt: "Die einschlägigen Regelwerke erlauben bis zu zehn Millimeter Abweichung." Diese für Wessel charakteristische Präzisionsarbeit bedeutete für die Georgsmarienhütte einen deutlich geringeren Kostenaufwand beim anschließenden Ausmauern der Pfanne.
Brennen statt Fräsen oder Wasserstrahl-Schneiden
Überaus zufrieden ist Stefan Biniszkiewicz mit seiner Entscheidung für Jebens und das von dem Brennschneidspezialisten entwickelte Verfahren des 3D-Brennens als Ersatz für teure Fräsbauteile. Auf der BAUMA 2016 hatte diese Technik am Stand von Jebens sein Interesse geweckt. Als er ein Jahr später die hohen Angebote für die Fertigung der Stahlrippen als Fräsbauteile oder per Wasserstrahl-Schneiden erhielt, erinnerte er sich an den Spezialisten aus Süddeutschland und bat Jebens um ein Vergleichsangebot. Die Ersparnis von 6.000 Euro pro per Brennschneidroboter gefertigter Rippe sprach eindeutig für diese 3D-Brennschneid-Lösung. Für den Dickenabtrag setzt Jebens eine Sato-Brennmaschine ein, für das anschließende Finishing der Geometrien auf verschiedenen Ebenen einen Fasroboter. So fertigt das Unternehmen nur mit der Flamme exakt nach Kundenvorgabe sogar enge Radien oder Ausklinkungen mit unterschiedlichen Schnitthöhen und -breiten. Folglich sind auch Schnitte, deren Winkel sich entlang der gesamten Schnittkante kontinuierlich verändern, wie sie die konische Pfannenform für die Stahlrippen erforderte, mit dieser Technik sicher und reproduzierbar realisierbar. Carsten Schmickler, Geschäftsführer von Jebens, erklärt: "Auf klassischen Brennschneidmaschinen ist die Schnittführung beim mehrlagigen Brennen begrenzt, da die Brennteile dafür immer wieder gedreht werden müssen und nur ein gleichbleibender Winkel entlang der Schnittkante möglich ist". Jebens verstellt den Brenner am Roboter und kann dadurch auch anspruchsvolle Geometrien per 3D-Schnitt realisieren. Die Anforderungen von Wessel waren allerdings so komplex, dass man in Korntal-Münchingen den Roboter zusammen mit dem Hersteller der Steuerungssoftware entsprechend programmieren musste. So wurde es möglich, den Schnittwinkel bei den 120 x 245 x 928 Millimeter großen Rippen über die Bauteillänge von 72 auf 84 Grad zu vergrößern. Dadurch konnte Jebens die Rippen als ein um eine imaginäre Längsachse gedrehtes Brennteil mit vorgegebener Torsion produzieren. Voraussetzung dafür war allerdings auch die ausgeprägte Expertise in Brenner- und Temperaturführung. Da ein Brenner nicht mit der Präzision eines Lasers arbeitet, musste vor der Bearbeitung jedes Teil mit produktspezifischen Parametern vorgeglüht werden, um eine Rissbildung zu vermeiden. Die exakte Schnittführung hatte Jebens zuvor anhand von per 3D-Simulation erstellten Modellen ermittelt, da es in der Realität keinen zweiten Versuch gibt. Anhand der von Wessel übermittelten Zeichnungen wurden so alle 28 Rippen mit auf den jeweiligen Ausdehnungskoeffizienten angepasster Brennerführung gebrannt.
Für Stefan Biniszkiewicz bot dieses Verfahren den zusätzlichen Vorteil, dass die von der fast linienförmigen, zylindrischen Schneidflamme gefertigten Bauteile geometrisch sogar besser auf die Kegelkontur der Gießpfanne passen als vom Walzenfräser erstellte. Bereits in der Angebotsphase hatten ihn die Experten von Jebens durch gezielte Anmerkungen und Verbesserungsvorschläge von ihrer Fachkompetenz überzeugt. Da Jebens - dank der Zugehörigkeit zu Dillinger - obendrein die benötigten Bleche in allen erforderlichen Wandstärken vorrätig und damit entsprechend kurze Lieferzeiten hatte, beauftragte Wessel den Brennschneidspezialisten auch mit der Anfertigung aller anderen Brennteile für die Gießpfanne. Die hohe metallurgische Reinheit der Bleche erlaubte es zudem, durch zusätzliche Prüfungen kurzfristig das exakt benötigte Blech zu erhalten. Auch dabei bewies Jebens eine für Stefan Biniszkiewicz "geniale Flexibilität": Für die vom Auftraggeber vorgeschriebene Alterungsprüfung schnitt der Spezialist kurzerhand ein Stück aus dem vorhandenen Blech heraus und erhielt so binnen einer Woche das Prüfungsergebnis von der Materialprüfungsanstalt (MPA) Universität Stuttgart. Als dieses Material im Projektverlauf ein weiteres Mal benötigt wurde, war auch das kein Problem. "Jebens hatte das Material aufbewahrt, sodass wir wiederum binnen einer Woche das nachträglich bestellte Teil hatten", erinnert sich Stefan Biniszkiewicz.
Viel Potenzial bei anspruchsvollen Schnitten aus dem Vollen
Generell ist er voll des Lobs über die Zusammenarbeit: "Jebens ist kein reiner Zulieferer, sondern fertigt selber und denkt deshalb den Prozess über den eigenen Auftrag hinaus weiter." Das zeigte sich für ihn im gesamten Projektverlauf an der offenen Kommunikation und lösungsorientierten Zusammenarbeit - auch in Phasen mit unvorhergesehenen Schwierigkeiten. Besonders überzeugend war für ihn jedoch die Konfektionierung der Brennteile: "Jedes Bauteil war nicht nur nach Zeugnis gestempelt, sondern mit der genauen Positionsnummer verwechslungssicher beschriftet und sogar entgratet." So passte für ihn in der Zusammenarbeit mit Jebens einfach alles: Das innovative Verfahren hat gehalten, was er sich davon versprochen hat, Termintreue und Qualität waren optimal. "Ich habe mich als Kunde nie allein gelassen gefühlt, sondern für mich war die Zusammenarbeit mit Jebens ein Rundum-sorglos-Paket", stellt Stefan Biniszkiewicz anerkennend fest. Deshalb ist er auch bereits mit neuen Anfragen an den Brennschneidspezialisten herangetreten, denn insbesondere das 3D-Brennen ist aus seiner Sicht ein hochinteressantes Zukunftsthema: "Gerade im Bereich Hütten- und Kraftwerke sehe ich viele Möglichkeiten, wo man Schweißkonstruktionen aus dem Vollen als integral gebranntes Bauteil schneiden kann - und dadurch sehr viel Zeit und Geld spart."
Jebens GmbH Als ein führender Spezialist für schwere Brennteile, mechanische Bearbeitung und geschweißte Konstruktionen mit Stückgewichten von bis zu 160 Tonnen, setzt die Jebens GmbH mit Standorten in Korntal-Münchingen und Nördlingen regelmäßig Standards. Mit einer siebenstufigen Fertigung von Produkten in Dickenbereichen von 8 bis 1.400 mm, Breiten bis 5.000 mm und Längen bis 20.000 mm steht Jebens für Maßarbeit in Stahl. Als Tochterunternehmen des bedeutendsten Grobblechherstellers der Welt, der Gruppe Dillinger Hüttenwerke / GTS, hat Jebens jederzeit Zugriff auf technologisch richtungsweisendes Stahl-Know-how. Führende Technologie, modernste Maschinen und Anlagen, sowie der größte Glühofen Süddeutschlands, machen Jebens zum Experten für anspruchsvolle Aufgaben.




Quelle und Fotos: Jebens GmbH
Bildtexte (Vorschaubild): 3,90 Meter hoch mit fast 3,80 Meter im Durchmesser ist die Pfanne ein großes Kaliber.
Bild 1: Der Pfannenboden mit den Löchern für Temperaturmesssonde, Abstich und Gasspülung.
Bild2: Neben den Rippen mit gewollter Torsion fertigte Jebens auch die Fußteile der Pfanne.
Bild3: Die beiden 700 Kilogramm schweren, geschmiedeten Tragzapfen.
Bild4: Insgesamt fertigte Wessel fast 550 Kilogramm Schweißnaht für die Gießpfanne.
Bild5: Die Fertigungsvorrichtung senkt die Zeiten, in denen der auf dem Gerüst liegenden Schweißer in Zwangslage schweißen muss.