Zerspanung bleifreier Metalle – seit RoHS ein dringendes Thema
von Hubert Hunscheidt
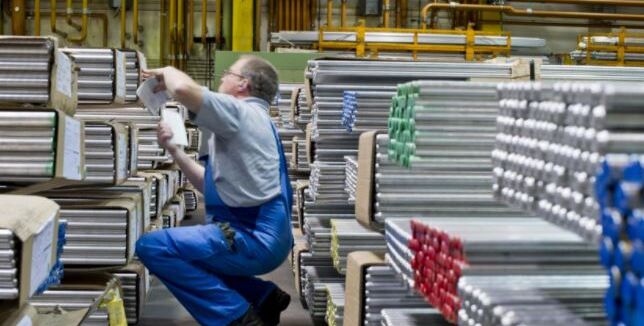
Müssen zukünftig alle metallischen Komponenten in Elektro- und Elektronikgeräten bleifrei sein? Die Frage kann erst beantwortet werden, wenn die EU-Kommission den Verlängerungsantrag der für die zerspanende Industrie äußerst relevanten Ausnahmeregelungen 6 a-c bearbeitet hat. Fakt ist: Mit Aluminiumwerkstoffen scheint der Schritt in die Bleifreiheit durchaus möglich – auch unter wirtschaftlichen Aspekten. Deutlich problematischer wird es bei Messing und Automatenstählen.
Ende Juli 2021 sind die Ausnahmen 6a, b und c der RoHS-Verordnung (2002/95/EG) ausgelaufen. Für die metallverarbeitende Industrie geht es erstmal weiter wie bisher: Solange es keine neue Regelung gibt, verarbeiten sie auch weiterhin Stähle, Aluminium- und Messingwerkstoffe, die Blei in geringen Mengen enthalten. Wie lange das noch so bleiben wird, ist offen – die Bewertung der Anträge auf Verlängerung hat das von der EU beauftragte Öko-Institut vor kurzem an die EU-Kommission zurückgeschickt, die nun entscheiden muss.
Die Frage, ob und wie Blei in metallischen Werkstoffen ersetzt werden kann, ist nicht eindeutig zu beantworten. Welche Probleme und Auswege es geben kann, erklären zwei Mitglieder des Verbands der Deutschen Drehteile-Industrie: Florian Heinrichs, Geschäftsführer der Heinrichs & Co. KG, und Simon Heil, Geschäftsführer der Grieshaber GmbH & Co. KG. Beide fertigen unterschiedliche Präzisionsdrehteile, unter anderem für die Automobilindustrie, und müssen den Spagat zwischen Prozesssicherheit und Wirtschaftlichkeit bei der Bearbeitung bleifreier Metalle auch heute schon meistern.
Ohne Verluste geht es nicht
Dürfte er nur noch bleifreie Stähle verarbeiten, sieht Florian Heinrichs vor allem die Prozesssicherheit massiv gefährdet. In seinem Hunsrücker Unternehmen, der Heinrichs & Co. KG, entstehen über 100 Millionen Drehteile jährlich, in mehr als 2.000 Varianten – vom Prototyp bis zur Großserie. Die Verschlussschrauben, Entlüftungsventile, Düsen und andere Abdichtlösungen kommen später in Fahrzeugen, Maschinen und Industrieanlagen zum Einsatz. „Besonders bei Automatenstählen können wir auf Blei im Moment nicht verzichten“, erklärt Heinrichs. Das Schwermetall ist relativ weich und hat eine niedrige Schmelztemperatur. Es erleichtert dadurch den Spanbruch, bildet einen Schmierfilm, reduziert die Zerspanungskräfte und schont die Werkzeuge. Für Heinrichs sind jedoch nicht die Standzeiten ausschlaggebend. „Hier liefern mittlerweile alternative Substrate und Beschichtungen, die in den vergangenen Jahren entwickelt und erprobt wurden, ähnlich gute Ergebnisse wie Blei“, erklärt er. „Das Hauptproblem ist der Spanbruch. Sobald sich Späneknäuel oder zu lange Späne bilden, ist der Prozess nicht mehr sicher.“ Das gelte besonders für hocheffiziente Maschinen wie die Mehrspindeldrehautomaten. Denn hier ist die Gefahr noch höher, dass sich Späne um die rotierenden Werkzeuge wickeln und einen Werkzeugbruch verursachen. „Für uns ist das nicht akzeptabel, da wir eine Null-Fehler-Politik fahren“, ergänzt Heinrichs.
Dennoch zerspant Heinrichs & Co. KG auch heute schon bleifreie Stähle – sobald Kunden RoHS-konforme Neuteile anfordern. „Mit viel Aufwand kann man vieles machen“, kommentiert der Geschäftsführer und deutet damit an, dass der Verzicht auf Blei in Automatenstählen auf Kosten der Wirtschaftlichkeit, Nachhaltigkeit und Effizienz geht.
Was es für die Zerspanung der bleifreien Stähle auf jeden Fall braucht, sind computergesteuerte Drehmaschinen. Sie können – anders als kurvengesteuerte Anlagen – in Zusatzzyklen automatische Spanbrecher-Stopps fahren. Das Problem ist jedoch, dass nicht jeder Drehteilehersteller sofort auf die CNC-Bearbeitungszentren umstellen kann: Heinrichs geht deutschlandweit von einem sehr hohen Bestand an konventionellen Drehmaschinen aus – diese auf die Schnelle zu ersetzen, ist weder nachhaltig noch sinnvoll. „Wir schätzen ja auch unsere zuverlässigen kurvengesteuerten Anlagen, da sie produktiver als mach ein CNC-Spindler sind. Allein die durch den geringeren Output entstehenden Mehrkosten von circa 30 Prozent, wird kein Endkunde akzeptieren“, erklärt er.
Eine Frage der Argumente
Für Florian Heinrichs ist klar: noch braucht es die Ausnahme 6a der RoHS-Richtlinie. Entsprechend gespannt ist er auf die Entscheidung aus Brüssel. Die Verlängerungsanträge wurden von einem industrie- und branchenübergreifenden Verbändenetzwerk, zu dem auch der Verband der Deutschen Drehteile-Industrie zählt, erarbeitet und Anfang 2020 fristgerecht – 18 Monate vor Ablaufdatum – bei der EU-Kommission eingereicht. Diese hat das Öko-Institut damit beauftragt, die Anträge fachlich und technisch zu bewerten. Auch das ist in den vergangenen Monaten passiert und der Endbericht liegt nun bei der EU-Kommission. Welche Empfehlung die unabhängige Forschungs- und Beratungseinrichtungen hinsichtlich künftiger Ausnahmen gegeben hat, ist nicht bekannt. Mit entscheidend hierfür sind die Argumente, die die Branche vorbringen kann – und die sind unterschiedlich schlagkräftig. So scheint es für die Ausnahme 6b – sie regelt den Bleigehalt in Aluminiumwerkstoffen – eher wenig neue Argumente zu geben.
Warum das so ist, macht Geschäftsführer Simon Heil deutlich. Die Grieshaber GmbH zerspant bis zu 3.500 Tonnen Aluminium pro Jahr und ist ein Experte auf diesem Gebiet. Als 2003 die erste RoHS-Richtlinie den Bleianteil in Aluminiumwerkstoffen von 1,5 auf 0,4 Prozent reduzierte, war das ein Weckruf für das Schwarzwälder Familienunternehmen. Es startete Projekte zur systematischen Werkstoffkunde und holte auch namenhafte Hersteller von Aluminiumstangen mit ins Boot, die unter anderem folgende Fragen bearbeiteten: Wie kann Blei in Aluminiumwerkstoffen reduziert und substituiert werden? Welche Legierungen und Legierungselemente haben welche Eigenschaften? Welche Auswirkungen hat das auf den Bearbeitungsprozess sowie das fertige Drehteil? Mit den Ergebnissen der theoretischen und praktischen Arbeiten bauten die Projektingenieure eine interne Werkstoffdatenbank auf und gewannen wertvolles Know-how. „Von der fundamentalen Projektarbeit profitieren wir bis heute. Wir arbeiten immer noch mit dieser Datenbank und kooperieren weiterhin intensiv mit den Herstellern. So können wir unsere Kunden optimal beraten, wenn es um den Einsatz bleifreier Materialien geht“, betont Heil.
Die Versuche mit den neuen Legierungen zeigen, dass mittlerweile auch die bleifreien Varianten beherrschbar sind – mit entsprechenden Modifikationen am Prozess und am Werkzeug. Denn wie beim Automatenstahl erzeugt auch beim Aluminium der Wegfall von Blei unter anderem längere Späne, mehr Wärme am Werkzeug, einen höheren Schnittdruck und größeren Werkzeugverschleiß. Bei dünnwandigen Bauteilen nahm durch den Legierungswechsel zum Teil sogar die Rissgefahr zu, bemerkten die Techniker.
Umdenken – und in CNC investieren
Um diese Probleme in den Griff zu bekommen, nennt Simon Heil mehrere mögliche Stellschrauben: In der Fertigung passen die Techniker Parameter Vorschübe, Drehzahlen sowie Schnittgeschwindigkeiten und Drücke an. Bei Bedarf wechselt Grieshaber das Kühlschmiermittel oder sogar das zugrundeliegende Verfahren – vom Drehen zum Fräsen oder eine Kombination daraus. Dennoch: „Späne, die sich um ein Werkstück wickeln, lassen sich nicht vermeiden. Das erfordert unter Umständen eine 100-prozentige, gegebenenfalls auch nachträgliche, Prüfung im Rahmen der Qualitätssicherung“, erklärt Heil. Bei Bauteilen, die in sicherheitsrelevanten Systemen von Fahrzeugen sitzen, beispielsweise Bremsen, ist das in der Regel kein Problem. Sie werden vorn vornherein genauestens kontrolliert und damit ist die Überprüfung auf Späne nur ein weiterer Punkt bei der Qualitätssicherung. Unabhängig davon gilt: „Wir müssen bauteilspezifischer denken und verschiedene Kniffe anwenden. Das geht kaum noch mit kurvengesteuerten Maschinen. Bleifreie Materialien brauchen flexiblere, CNC-gesteuerte Prozesse, da wir viel feinfühliger in die Prozessparameter eingreifen können“, ist Heil sich mit Heinrichs einig.
„Blei hat einem viel mehr verziehen. Aber natürlich ist die Zerspanung bleifreier Materialien möglich, wenn man das Know-how und einen entsprechend flexiblen Maschinenparkt hat“, fasst Heil zusammen. Dass das auf die Kosten gehen kann – aber nicht muss, wie der Geschäftsführer am Rande erwähnt – sei nachvollziehbar.
„Wenn wir Kundenanfragen bekommen, checken wir proaktiv, ob diese bezüglich der Materialauswahl zukunftsfähig sind. Enthält das Material noch Blei, schlagen wir einen alternativen Werkstoff vor und bieten an, ein entsprechendes Angebot zu erstellen. Dieses inkludiert auch eventuelle konstruktive Optimierungsvorschläge,“, erläutert Heil. Manche Kunden fragen auch von sich aus nach neuen Materialien: Sie nutzen die Chance der bei Neuentwicklungen oder Zeichnungsänderungen sowieso erforderlichen Bemusterung, um sich mit einer bleifreien Alternative zukunftssicher aufzustellen. „Die Reise geht eindeutig in Richtung bleifrei. Diesen Zug können wir nicht aufhalten – das haben wir früh erkannt und darauf reagiert. Bleifrei bringt hier niemandem mehr aus der Ruhe“, resümiert Heil.
Bearbeiter von Automatenstählen sind dagegen nicht so entspannt. Florian Heinrichs weiß, dass es den Druck braucht: „Keiner ändert etwas, was funktioniert, wenn es nicht notwendig ist.“ Er plädiert aber für einen ausreichend langen Umstellungszeitraum, der sich an den Investitionszyklen und nicht an Verfallsdaten von Ausnahmeregelungen orientiert. „Wir brauchen Planungssicherheit und Toleranz. Mit den neuen Prozessen startet eine neue Lernkurve. Das bedeutet auch, dass Fehler in Kauf genommen und akzeptiert werden müssen“, sagt Florian Heinrichs abschließend.
Quelle und Fotos: Verband der Deutschen Drehteile-Industrie im Fachverband Metallwaren- und verwandte Industrien (FMI) e.V.