Werkzeuge und Formen in der Druckgießtechnik
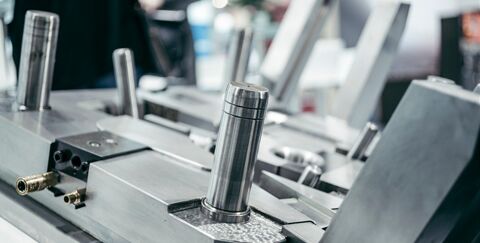
Nürnberg - Druckgießen ist ein Formgebungsverfahren für die Serienproduktion von Werkstücken aus Aluminium, Zink, Magnesium, Kupfer, Blei, Zinn und deren Legierungen. Der Gießvorgang erfolgt in Druckgießmaschinen, die in Warmkammer- und Kaltkammer-Gießmaschinen unterteilt werden. Der wesentliche Unterschied besteht darin, dass der Behälter mit der Metallschmelze bei Warmkammer-Gießmaschinen in der Maschine, im anderen Fall außerhalb von ihr angeordnet ist. In beiden Arten von Maschinen wird das schmelzflüssige Metall aus einer Gießkammer über einen oder mehrere Gießkanäle in den Hohlraum einer stählernen Dauerform gedrückt, wo es die von der Form vorgegebenen Konturen annimmt und erstarrt.
Damit das Gussteil aus der Form entnommen werden kann, bestehen diese Druckgießformen aus zwei Hälften. Die eingussseitige Formhälfte ist an der starren Seite der Druckgießmaschine auf einer festen Aufspannplatte montiert, die auswerferseitige Formhälfte auf der anderen Seite auf einer beweglichen Platte. Die Hälften werden vor dem Schließen mit einem Trennmittel besprüht, damit sich später das Gussteil leicht von der Form lösen lässt und die Platten sich nicht überhitzen. Je nach Größe der Gussteile können bis zu 300 Gießzyklen je Stunde durchgeführt werden.
Extreme Belastungen
Bei geschlossener Form wird die Schmelze unter einem Druck von bis zu 1.200 bar in die Form gedrückt, wobei sie Formfüllgeschwindigkeiten von maximal 150 m/s (540 km/h) erreicht. Große Schließ- und Zuhaltekräfte sind nötig, um die Formhälften aneinander zu pressen und die Formen geschlossen zu halten: In Warmkammer-Gießmaschinen wirken bis zu 8.000 kN (800 t), in Kaltkammer-Gießmaschinen bis zu 45.000 kN (4.500 t). Die verwendeten Formen müssen werkstoff- und konstruktionstechnisch so ausgelegt sein, dass sie die mit großen Schmelzemengen verbundenen Belastungen dauerhaft ertragen. Ist das Metall erstarrt, öffnen sich die Formhälften, und das Gussteil wird von Bolzen ausgestoßen oder von einem Roboter entnommen und zur Weiterbearbeitung befördert.
Hochleistungsstähle
Eine zentrale Bedeutung für den Druckgießprozess hat die Form. Sie gibt die Konturen vor, die auf das Gussteil übertragen werden. Sie soll außerdem dazu beitragen, dass das Gussteil möglichst rasch erstarrt. Dadurch wird die Bildung eines feinkörnigen Gefüges gefördert, was der Gussteilqualität zugute kommt. Um eine optimale Kühlung zu erreichen, werden die Formen an bestimmten Stellen gekühlt. Ein weiterer Effekt ist, dass, die Herstellungszeit verkürzt wird, was wirtschaftliche Vorteile mit sich bringt. Der Aufbau von Druckgießwerkzeugen ist in der Norm DIN 16760-1 beschrieben. Die am Druckgießvorgang beteiligten Werkzeuge sind naturgemäß hohen thermischen und mechanischen Belastungen ausgesetzt und müssen diesen dauerhaft standhalten. So erreichen Formen für den Zinkdruckguss beispielsweise Standzeiten von 500.000 bis zwei Millionen Zyklen.
Um derartige Leistungen zu erreichen, werden die Druckgießwerkzeuge, zu denen außer den erwähnten Formen auch Formeinsätze, Kerne, Schieber und Auswerfer gehören, aus hochfesten Warmarbeitsstählen wie X40CrMoV5-1 (1.2344) oder Sonderwerkstoffen, zum Beispiel Hartmetallen, hergestellt. Eigenschaften, die bei diesen Werkzeugen eine sehr wichtige Rolle spielen, sind hohe Verschleißfestigkeit, hohe Duktilität, hohe Warmfestigkeit, hohe Warmriss- und Warmverschleißbeständigkeit sowie eine gute Wärmeleitfähigkeit.
CAD/CAM-Systeme
Früher wurden Werkzeuge für die Druckgießtechnik nach Zeichnung gefertigt, heute arbeiten Konstrukteure mit 3D-CAD-Daten und nutzen zeitgemäße IT-Technologien. Bei der Konstruktion von Gießformen sind sowohl der Gießvorgang – und damit der Schmelzefluss und die Kühlung – als auch die Geometrie und die Abmessungen der zu fertigenden Druckgussteile zu beachten. Die Gussteile sollen sich durch ein gleichmäßiges, feinkörniges Gefüge, hohe Maßgenauigkeit und Maßhaltigkeit und eine hohe Oberflächenqualität auszeichnen.
Computer-gestützte Simulationsberechnungen helfen, die Werkzeuge optimal auf das jeweilige Gussteil abgestimmt zu gestalten. Zur Fertigung nutzen Werkzeug- und Formenbauer CAM-Systeme. Die formgebenden Konturen werden in den Formwerkstoff durch CNC-gesteuerte Fräsmaschinen sowie Senk- und Schneiderodiermaschinen mit hoher Präzision eingearbeitet. Die Fertigung der Formen ist sehr aufwendig und damit kostspielig.
Bis zu 20 % der Kosten eines Werkstücks aus Aluminiumdruckguss entfallen auf das Werkzeug. Für die Herstellung von Bauteilen in großen Serien ist dies ab einer gewissen Losgröße jedoch kostengünstiger, als die Teile auf andere Weise, zum Beispiel durch spanabhebende Verfahren, herzustellen. Außerdem ist die Fertigungszeit für jedes Teil kürzer. Eine standardisierte, zeitsparende Vorgehensweise zur Konstruktion von Druckgießwerkzeugen wurde am Institut für Maschinenkonstruktion der Universität Magdeburg entwickelt.
Noch sehr viel Potenzial
Die Stähle, die zur Konstruktion und Simulation vorgesehenen Software-Programme und die Fähigkeit der Bearbeitungssysteme sind Gegenstand ständiger Weiterentwicklung. Auch den Themen „Digitalisierung“ (Industrie 4.0) und „3D-Druck“ erfahren wachsende Bedeutung. Fachmessen greifen diesen Trend auf. Die EUROGUSS widmet diesem in der Sonderschau „Additive Fertigung“ besonderes Augenmerk.
Durch digitale Techniken lassen sich Prozesse effizienter steuern und Optimierungspotentiale besser erkennen. Mit 3D-Druckverfahren („additive manufacturing“) können Teile hergestellt werden, die auf konventionelle Weise nicht gefertigt werden können, beispielsweise komplex geformte Einsätze für Druckgussformen, in die konturnahe, gekrümmt verlaufende Kühlkanäle integriert sind.
Nach Ansicht von Dr.-Ing. Ioannis Ioannidis, Präsident und CEO des Druckgießmaschinenherstellers Oskar Frech und Vorstandsvorsitzender im Fachverband Gießereimaschinen und Vorstandsmitglied der Arbeitsgemeinschaft Additive Manufacturing im VDMA, gibt es für den Formenbau in diesem Bereich noch sehr viel Potential: „Der gesamte Wärmehaushalt in der Form kann in der Weise beeinflusst werden, dass die Form zum Beispiel vor Verschleiß besser geschützt wird und die Beschaffenheit des zu gießenden Teils beeinflusst werden kann.“
Die Fachmesse EUROGUSS 2020
Einen Einblick in den Stand der Druckgießtechnik und Anregungen, wie Druckgießereien ihre Marktstellung stärken und ausbauen können, aber auch rund um Ressourceneffizienz und Umweltschutz, gibt die Internationale Fachmesse für Druckguss EUROGUSS, die vom 14. bis zum 16. Januar 2020 in Nürnberg stattfindet.
Quelle: NürnbergMesse GmbH https://www.nuernbergmesse.de / https://www.euroguss.de/de
Vorschaubild: Gebrüder Nelles Werkzeugbau GmbH, Sankt Augustin