Stahlwerke leben die digitale Transformation
von Hubert Hunscheidt
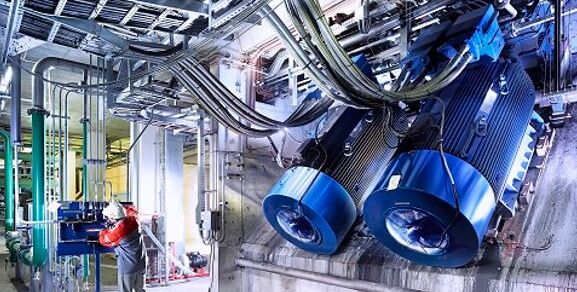
Nicht disruptiv neue Geschäftsmodelle stehen auf der Agenda von Stahlwerken, sondern in erster Linie Ergebnisverbesserungen und eine Ausweitung der Serviceleistungen. Neue Digitalisierungslösungen − von der Transformation des Hochofens bis zur Vision des autonomen Stahlwerks, vom digitalen Schmelzbetrieb bis zur Gießerei 4.0 werden einen Schwerpunkt der kommenden Metallurgie-Fachmessen GIFA, METEC, THERMPROCESS und NEWCAST bilden, vom 12. bis 16. Juni 2023 in Düsseldorf.
In der hochautomatisierten Stahlindustrie spielen Daten schon lange eine tragende Rolle. Am Beispiel ThyssenKrupp Steel: Allein das Warmbandwerk 2 in Duisburg verarbeitet täglich neben rund 16 500 Tonnen Stahlbrammen auch die Daten von mehr als 1,2 Milliarden Messungen. Begriffe wie „Big Data“, „Digitaler Zwilling“ und „Machine Learning“ gehören heute zum Jargon der Metallurgen wie „Abstich“ und „Brammenguss“. Spezialisten künstlicher Intelligenz (KI) und App-Programmierer ergänzen traditionelle Berufsbilder wie Hochöfner und Warmwalzer. Der digitale Zwilling bildet die gesamte Produktion ab und kann im Abgleich mit dem realen Stahlstandort für alle Teile der Wertschöpfung von Produkten, Anlagen und Dienstleistungen genutzt werden. Ein Kernziel besteht darin, Produkt- und Maschinendaten über verschiedene Prozessstufen hinweg auszuwerten. Mithilfe von Data Analytics lassen sich beispielsweise Materialeigenschaften wie Dickenschwankungen, Rauheiten oder Festigkeiten präziser vorhersagen und Toleranzen genauer treffen. Abertausende Sensoren erfassen dazu die Qualitäts- und Produktionsdaten über die gesamte Prozesskette der Flachstähle. Die Datenbasis bildet das Fundament, um Produktionsprozesse in Echtzeit zu steuern und zu analysieren. So werden beispielsweise in der Feuerbeschichtungsanlage 8 von ThyssenKrupp Steel in Dortmund mit den Ergebnissen der Daten-Auswertung mathematische Modelle erstellt, um damit das Dressiergerüst zu steuern. Das Datenmodell lenkt die Anlage so, dass die angepeilten Rauheitswerte der Stahlbänder einhalten werden und dass sich die Fahrweise bei Bedarf online nachjustieren lässt. Dadurch erschließt sich der Stahlerzeuger die Möglichkeit neuer Service-Leistungen. Lothar Patberg, Leiter Innovation bei thyssenkrupp Steel: „Ein Kunde könnte künftig nicht nur den aktuellen Status seines Auftrags nachvollziehen. Er könnte auch ausgewählte Qualitätsdaten aus der Produktion erhalten, um bereits vor der Auslieferung des Coils eigene Prozesse anzupassen.“
Der Technologiewechsel auf CO2-freie Produktion mit Wasserstoff und erneuerbaren Energien verleiht dem Einsatz digitaler Technologien zusätzlichen Schwung. Laut der Unternehmensberatung Accenture ließen sich in der industriellen Fertigung bis zu 61 Megatonnen CO2 bis 2030 durch Digitalisierung einsparen. Metallurgische Anlagenbauer wie SMS, Primetals und Danieli haben das Potenzial längst erkannt: Zur Stärkung des eigenen Unternehmens, vor allem aber zur Eröffnung neuer Geschäftsfelder.
SMS digital: Die Großen entwickeln den Markt
Ein Pionier der Digitalisierung und Aussteller auf der METEC 2023 ist die Düsseldorfer SMS group. Automatisierungstechnik gehört seit vielen Jahren zur DNA des metallurgischen Anlagenbauers. Technologien wie Virtual Reality (VR), Augmented Reality (AR) und Digital Twin (digitaler Zwilling) nutzten die Ingenieure in der Stahlwerksentwicklung lange bevor Industrie 4.0 als Trendbegriff aufkam. Wurden früher einzelne Betriebsteile wie das Walzwerk automatisiert, so vernetzt Digitalisierung die gesamte Produktion vom Hochofen bis zum fertigen Produkt auf allen Ebenen. Das Potenzial der Digitalisierung für die Entwicklung neuer Geschäftsfelder erkannte SMS als einer der ersten in der Branche und gründete 2017 das Startup SMS digital. Was mit 10 Mitarbeitern in einem Hinterhof begann, ist heute als SMS Digital GmbH mit international mehr als 350 Spezialisten das führende Softwareunternehmen im Metallurgie-Bereich. Als Chief Digital Officer im Vorstand der SMS group verantwortet seit 2018 die promovierte Ingenieurin und ehemalige Hochschulprofessorin Katja Windt die Schlüsselbereiche der digitalen Transformation − im eigenen Unternehmen und beim Kunden. Im metallurgischen Prozessknowhow aus 150 Jahren Anlagentechnik sieht die Digitalisierungschefin der SMS einen entscheidenden Vorteil gegenüber dem Wettbewerb, vor allem gegenüber Startups oder potenziellen Eindringlingen wie den digitalen Champions Google oder Amazon, die längst ein Auge auf die Industrie geworfen haben. Digitalisierung zur Prozessoptimierung und für das Energiemanagement ist ein wesentlicher Bestandteil auch der neuen Geschäftsfelder der SMS group. Als global Player für die Reduzierung von Kohlendioxidemissionen und Circular Economy investiert der Anlagenbauer erfolgreich in Dekarbonisierungs- und Recycling-Technologien, von der klimaneutralen Stahlproduktion mit Wasserstofftechnologien über Batterierecycling und Urban-Mining-Lösungen für die Edelmetallrückgewinnung aus Elektroschrott bis zu Anlagen zur Produktion von grünem Synthesegas und synthetischen Kraftstoffen.
Big River Steel: Das lernende Stahlwerk ist erst der Anfang
Im Fokus der Digitalisierung steht die Stahlindustrie. Bereits zur METEC 2019, Internationale Metallurgie-Fachmesse mit Kongressen, konnte der Anlagenbauer mit Big River Steel das weltweit erste „lernende Stahlwerk“ vorstellen. Das von SMS in den USA errichtete und in Zusammenarbeit mit dem Kooperationspartner Noodle.ai digitalisierte und mit künstlicher Intelligenz (KI) ausgerüstete Werk wird so ressourcenschonend und energiesparend wie heute möglich betrieben. Die KI von Noodle.ai analysiert historische Daten und zum Teil hochfrequent aufgelöste Signalreihen von mehr als 50 000 Sensoren. Die KI-Plattform nutzt zusätzlich zu den Daten des Stahlwerks auch externe Datenquellen, die Produktionsabläufe erfassen, vorhersagen und Korrekturmaßnahmen vorschlagen. Künstliche Intelligenz hilft somit, die Ausbringung zu maximieren, die Produktqualität zu verbessern und Sicherheitsrisiken auszuschalten. Eine immense Datenmenge, aus der mit KI Wissen generiert wird und mit dessen Hilfe BRS kostengünstiger und schneller hochwertige Stahlprodukte herstellen kann. Das lernende Stahlwerk in den USA ist erst der Anfang. Das Ziel ist für Digitalchefin Windt die selbststeuernde Produktion: Ein mit Hilfe lernender Algorithmen autonom operierendes Stahl- oder auch Aluminiumwerk. Kernprodukt für die Digitalisierung ist im SMS-Digitalbaukasten die sogenannte Data Factory, die Sensordaten sammelt und aufbereitet. An diese Softwareplattform lassen sich je nach Kundenwunsch und angestrebter Performance-Steigerung die unterschiedlichsten Applikationen andocken. In der herkömmlichen Produktion werden fertige Produkte auf Mängel untersucht. Bei fehlerhafter Ware beginnt die Ursachensuche, die Fehlerquelle muss abgestellt werden. In der Industrie 4.0-Logik werden durch stetige Überwachung der Produktion Fehler verhindert, bevor sie auftreten. Das spart Zeit und Geld.
Der Kunde muss für die Leistung nicht zwingend neue Anlagentechnik kaufen. Als neues Geschäftsmodell bietet SMS neben dem Kauf „Equipment-as-a-Service“ an. „Der Kunde schließt mit uns einen Servicevertrag über eine Komponente, beispielsweise einen Teil eines Walzwerks oder eine Stranggießanlage“, erläutert Windt. Der Anlagenbauer verkauft in diesem Fall also nicht die Anlagentechnik, vielmehr zahlt der Kunde für deren Betrieb und die verwendeten Digitalapplikationen.
Die Stärke der Digitalisierung hat sich nicht zuletzt während der Corona-Pandemie gezeigt. So konnte SMS mit Hilfe seiner AR-Technologie Stahlwerke aus der Ferne in Betrieb nehmen, ohne dass wie üblich ein Servicetechniker vor Ort zu sein brauchte.
Smart Steel Technology: Startup in Angriffstellung
Den Energieverbrauch und den Ausstoß klimaschädlicher Gase wie Kohlendioxid bei der Stahlproduktion mit Technologien wie Künstlicher Intelligenz (KI) und Maschinelles Lernen (Machine Learning, ML) zu senken, verspricht Smart Steel Technology (SST). Das 2017 von dem Mathematiker Dr. Falk-Florian Henrich in Berlin gegründete Startup hat sich Prozessoptimierung auf allen Ebenen auf die Fahne geschrieben. Dazu soll die Stahlindustrie von einer regelbasierten Produktion auf eine KI-basierte Produktion umstellen.
Stahlhersteller transformieren konventionelle Herstellungsprozesse in Richtung Energieeinsparung und CO2-Reduktion. Mit dem schrittweisen Wechsel des Reduktionsmittels von Kohle zu Wasserstoff werden die Kohlendioxid-Emissionen bereits am Hochofen reduziert. Hinzu kommen im Zuge der Dekarbonisierung der Stahlerzeugungsroute neue Verfahrenswege wie die Direktreduktion mit anfangs Erdgas und zunehmend Wasserstoff. Daher benötigten Stahlhersteller Lösungen zur Bewertung und Kontrolle der CO2-Effizienz aller Produktionswege sowie des CO2- und Energie-Fußabdrucks heruntergebrochen auf jedes einzelnen Stahlprodukt. Der Druck kommt nicht zuletzt vom Kunden. Der CO2-Fußabdruck wird in der Automobilindustrie zunehmend zum Beschaffungskriterium für Stahlprodukte. „Genaue Energie- und CO2-Daten ermöglichen es den Stahlherstellern, ihre Umstellungsbemühungen in Rechnung zu stellen und bei Audits erfolgreich zu sein. Automatisierte CO2- und Energieanalysen mit KI-basierten Modellen sind der Schlüssel“, sagt Henrich. Mit den KI-basierten Softwarepaketen von SST sei es möglich, Energieverbrauch und CO2-Ausstoß für jedes Flach- oder Langprodukt exakt zu dokumentieren und rückverfolgen zu können. Die KI berücksichtigt zahlreiche Einflussfaktoren auf die Energieeffizienz wie Rohstoffqualität, Produktmix und Wartung.
Von der Stärke seiner KI-Lösungen überzeugen konnte SST-Chef Henrich neben Unternehmen wie Feralpi und Vallourec den weltgrößten Stahlerzeuger ArcelorMittal. Beispiel Eisenhüttenstadt: Dort wurde mit Methoden der Künstlichen Intelligenz und Maschinellen Lernen eine Verbesserung der Oberflächenqualität bei hochwertigen Stahlsorten für die Automobilindustrie um mehr als 50 Prozent erreicht. Die KI-Software wird nicht nur zur Vorhersage der Oberflächenqualität eingesetzt, sondern auch um die Entstehung von Oberflächenfehler zu verhindern. Nach der erfolgreichen Erprobung in Eisenhüttenstadt hat ArclorMittal auch an den Standorten Bremen, Hamburg und Duisburg Software aus der SST-Familie installiert.
Fero Labs: Änderung der Rohmaterialienzusammensetzung in Echtzeit
Auch das US-amerikanische Startup Fero Labs will bei den Themen Dekarbonisierung und grüner Stahl punkten, wie Europa-Geschäftsbereichsleiter Tim Eschert versichert. KI-Software von Fero Labs ermögliche, in Echtzeit bei der Zusammensetzung von Rohmaterialien zu pendeln und damit die Wahrscheinlichkeit von Ausschuss im Produktionsprozess signifikant zu reduzieren: „Beim brasilianischen Stahlerzeuger Gerdau kommen wir bei einem mittleren Produktionsvolumen auf rund 9 Prozent Einsparungen im Jahr.“
Bildtext: ArcelorMittal treibt die Digitalisierung voran. Nach dem erfolgreichen Einsatz von Methoden künstlicher Intelligenz (KI) und maschinellem Lernen (ML) in Eisenhüttenstadt wurden auch die Werke in Hamburg, Bremen und -im Bild - Duisburg mit KI und ML optimiert.
Autor: Gerd Krause, Mediakonzept Düsseldorf
Quelle: Messe Düsseldorf GmbH / Foto: © Peter Ginter/ ArcelorMittal