Innovative Rohrsysteme für Offshore-Windkraftanlagen
von Alexander Kirschbaum
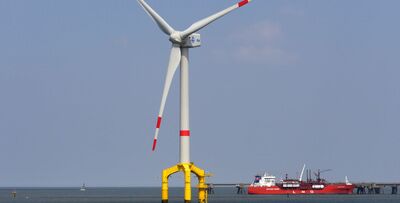
Stahlröhren oder Stahlrohrsysteme gehören bei den Fundamenten für Offshore-Windenergieanlagen (OWEA) zu den am häufigsten verwendeten Konstruktionselementen. Bei der Auswahl des Fundamenttyps spielt neben der Größe und dem Gewicht der OWEA vor allem die Wassertiefe eine Rolle, die in der Regel mit der Entfernung zum Festland wächst. Das Fraunhofer-Institut für Windenergie und Energiesystemtechnik in Kassel (IWES) gibt im Mitte 2015 publizierten „Windenergie Report Deutschland 2014“ an, dass die wichtigsten Offshore-Länder heute verstärkt auf einen Ausbau der Farshore-Leistung setzen, also auf Offshore-Standorte mit mindestens drei Seemeilen bzw. 5,5 Kilometer Küstenentfernung.
Vor allem in Deutschland werden die meisten Offshore-Windparks in größeren Wassertiefen und Küstenentfernungen realisiert, um die Meeresumwelt im Nationalpark Wattenmeer nicht zu beeinträchtigen. Laut IWES wurden 2014 global OWEA in durchschnittlich 21,1 Kilometer Küstenentfernung und 32,3 Meter Wassertiefe zugebaut. Deutsche Offshore-Anlagen stehen dagegen durchschnittlich in einer Küstenentfernung von 65 Kilometer und einer Wassertiefe von rund 29 Meter und damit im weltweiten Vergleich am weitesten von der Küste entfernt.
Große Vielfalt bei Gründungsstrukturen
Der Trend zum Bau von OWEA in zunehmend tieferen Gewässern hat einen großen Einfluss auf die verwendeten Gründungsstrukturen (mit Gründung bezeichnet man die Verankerung des Fundamentes im Meeresboden). Nach den zu Beginn genutzten Schwerkraftfundamenten und Einzelpfählen (Monopiles), kommen heute zunehmend weitere Strukturen zur Anwendung. Zu nennen sind neben den in Asien eingesetzten High-Rise-Pile Caps besonders Fachwerk-Tragstrukturen (Jackets), dreigliedrige Gründungsfundamente (Tripiles und Tripods), schwimmende Fundamente (Floating) sowie Saugpfahl-Fundamente und künstliche Inseln.
Dem IWES zufolge eignen sich die einzelnen Konstruktionen für unterschiedliche Standortbedingungen. Schwerkraftfundamente, Monopiles und High-Rise-Pile Caps stehen demnach vorwiegend in küstennahen und flachen Gewässern. Die Gründungsfundamente Tripod und Tripile liegen mit durchschnittlich 96,5 Kilometer in größter Entfernung zur Küste. Schwimmende Strukturen befinden sich mit durchschnittlich 78 Meter Wassertiefe noch in der Testphase. Zu den Monopiles ist aber ergänzend hinzuzufügen, dass deren Hersteller immer größere Exemplare entwickeln, die sich auch in entsprechend tieferen Gewässern einsetzen lassen.
Tripods: Dreibeinige Grundgerüste für Offshore-Windräder
Ein Tripod besteht aus drei im Winkel von 120 Grad zu einem Dreibein verschweißten Stahlrohren, auf denen ein Zentralrohr zentrisch aufgesetzt wird. Auf diesem Rohr wird der Turm montiert. Die Röhren der Beine haben Durchmesser von 1 bis 2,5 Metern und benötigen eine dreieckige Standfläche von 200 bis 300 Quadratmetern. Die Beine können aus jeweils einem Pfahl oder aus mehreren Röhren bestehen. An jedem Ende der Dreibeinkonstruktion sind zur Aufnahme der in den Meeresboden gerammten Fundamentpfähle wie bei Jackets Zentrierhülsen angebracht. Die Pfähle sind untereinander durch horizontale Streben verbunden und an das Zentralrohr über diagonale Abstrebungen angeschlossen.
Der Untergrund sollte eben und nicht zu steinig sein, weil die Konstruktion mittels Ramme mehrere Meter tief im Meeresuntergrund verankert wird. Tripods bieten eine hohe Standfestigkeit auch in rauen Seegebieten und sind nach dem heutigen Stand der Technik für Wassertiefen von 20 bis 80 Meter geeignet. Die eigens für die Offshore-Windenenergiebranche entwickelten Tripod-Fundamentstrukturen wurden erstmals 2009 bei der Errichtung des deutschen Offshore-Testfeldes „Alpha Ventus“ installiert.
Jackets: Stahlrohrfachwerke für große Tiefen
Schon seit Jahrzehnten haben sich Jackets als Gründungsstrukturen für Offshore-Plattformen auch bei großen Wassertiefen bewährt. Die Gründungsstruktur besteht hier aus einem aus Stahlrohren gebildeten räumlichen Fachwerk, ähnlich den Gittertürmen von Hochspannungsleitungen. Die vier Füße des Fundamentes enden in Hülsen, die die in den Meeresboden gerammten Fundamentpfähle aufnehmen. Jackets eignen sich wegen ihrer hohen Widerstandskraft für OWEA bis zu Wassertiefen von 70 Metern. Im Testfeld „Alpha Ventus“ kamen nicht nur Tripods zum Einsatz, sechs weitere Windräder wurden auf Jackets montiert.
Im Vergleich zu Tripod-Fundamenten soll ein Jacket rund ein Drittel weniger Stahl benötigen. Außerdem soll die fachwerkartige Gitterstruktur des Jackets Vorteile bei den Investitionskosten und im Bereich der Installationslogistik ergeben. Jackets weisen andererseits eine große Anzahl an Schweißverbindungen mit vielen Kanten und Verstrebungen auf, die wegen der erheblich höheren Korrosionsgefahr während der Betriebszeit regelmäßig gewartet werden müssen und so höhere Betriebskosten verursachen können.
Tripiles: leicht und kostengünstig
Wie Tripods wurden auch Tripile-Fundamente eigens für die Offshore-Windenergie entwickelt. Tripiles bestehen aus drei einzelnen Stahlrohren, denen an der Wasseroberfläche ein dreibeiniges Stützkreuz aufgesetzt wird, auf dem die Windkraftanlage montiert wird. Im Vergleich zu Monopiles haben die einzelnen Rohre einen geringeren Durchmesser und können einfacher gerammt werden. Tripiles werden mit Hilfe einer Ramm-Schablone im Meeresboden verankert. Anschließend wird den drei Stahlrohren in Höhe der Wasseroberfläche ein dreibeiniges Stützkreuz aufgesetzt, auf dem die Windkraftanlage montiert wird. Der Installationsvorgang gilt als relativ aufwendig, weil die Pfähle sehr präzise gerammt werden müssen, um das Stützkreuz genau aufsetzen zu können.
Tripiles eignen sich als Fundamente für Wassertiefen bis etwa 50 Meter und sind laut Herstellerangaben kostengünstiger und leichter als andere Gründungsstrukturen. Wanddicken und Längen der einzelnen Rohre sollen sich zudem individuell auf den Standort abstimmen lassen. Die ersten Tripiles wurden beim Offshore-Windpark BARD Offshore 1 in der Nordsee und bei der Nearshore-WEA Hooksiel realisiert.
Hexabase: Stahlrohrfundament mit sechseckigem Grundriss
Zwei aktuelle Entwicklungen bei OWEA-Gründungsstrukturen sind das Hexabase-Fundament und das darauf basierende Hybrid-Schwerkraftfundament Texbase. Hexabase, ein Stahlrohrfundament mit sechseckigem Grundriss, soll gegenüber herkömmlichen Bauformen große Vorteile aufweisen: effizienter und wirtschaftlicher bei der Produktion und Installation. Im Vergleich zu konventionellen Jackets oder großen Monopiles verspricht man eine Gewichtsersparnis von bis zu 20 Prozent und um ebenfalls bis zu 20 Prozent geringere Herstellkosten. Hinzu soll eine besonders gute Adaptierfähigkeit an unterschiedliche Wassertiefen und Windturbinentypen kommen. Die sechseckige Fachwerkkonstruktion, bestehend aus Rohren mit vergleichsweise geringen Durchmessern und Wanddicken, soll die dynamischen Kräfte der Windturbinen besonders gut aufnehmen können.
Laut thyssenkrupp ist eine wichtige Voraussetzung für die Realisierung der Vorteile, dass ein Großteil der verwendeten Rohre aus Warmbreitband hergestellt wird. Warmbreitband, mit einer maximalen Dicke von 25,4 Millimetern, soll sich deutlich leichter zu Konstruktionsrohren verarbeiten lassen als die bislang vorwiegend genutzten Quartobleche. Damit Schweißroboter die Rohre und Knotenpunkte vollautomatisch verbinden können, haben die geschweißten Rohre einen einheitlichen Durchmesser und die Knotenpunkte sind ebenfalls standardisiert. Das Verfahren verspricht nach Angaben der Entwickler eine schnelle und kosteneffiziente Produktion und durch den computergesteuerten Schweißprozess eine gleichbleibende Schweißnahtqualität.
Texbase: ein „leichtes“ Hybrid-Schwergewichtsfundament
Basierend auf dem Hexabase-Prinzip wurde mit Texbase ein Hybrid-Schwerkraftfundament entwickelt, das die Eigenschaften einer leichten Stahlbaustruktur mit der eines Schwerkraftfundaments vereint. Dabei wird eine Hexabase-Standardstruktur auf eine Basisstruktur mit Ballasttanks montiert, die aus besonders widerstandsfähigen wasserdurchlässigen Kunstfasergeweben bestehen und mit 2.000 bis 4.000 Tonnen Sand befüllt sind. Die Bodenauflage bildet ein Gerüst aus Stahlrohren, das mit Geotexil-Geweben bespannt wird und die Last gleichmäßig in den Untergrund einbringt.
Mit einem Gewicht von 450 bis 700 Tonnen vor der Installation ist Texbase ähnlich schwer wie ein herkömmliches Fundament. Das Fundament soll nur wenig Bodenvorbereitung benötigen und sich lärmarm mit einfachem Baugerät installieren lassen. Laut Entwicklungsgemeinschaft ist das neuartige Schwergewichtsfundament einerseits leicht transportabel, kann aber nach der Aufstellung auf dem bis zu 50 Meter tiefen Meeresgrund selbst bei den größten Windturbinen von mindestens 8 Megawatt Leistung einen sicheren Stand gewährleisten.
Quelle: Messe Düsseldorf Vorschau-Foto: Erich Westendarp/pixelio.de