Hybride Fertigungsprozesse sichern Wettbewerbsfähigkeit
von Angelika Albrecht
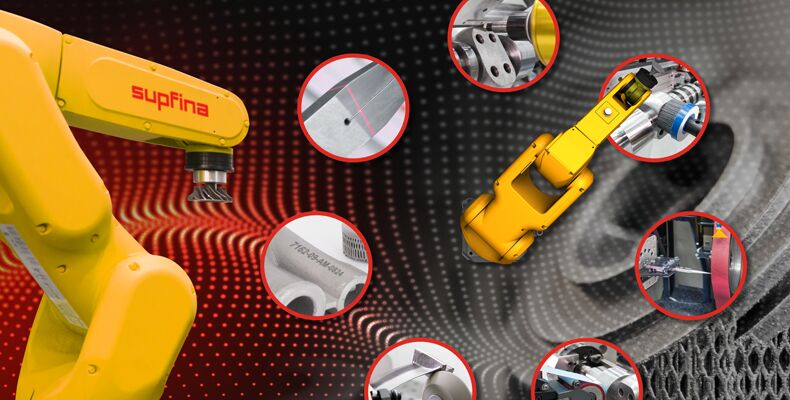
Fertigungsprozesse zu kombinieren, zahlt sich für produzierende Unternehmen häufig aus. Das gilt auch für die Schleif- und Feinbearbeitungstechnologien. Kommen moderne Automations- und Digitalisierungskonzepte hinzu, lassen sich deutliche Produktivitätssteigerungen für mehr Wettbewerbsfähigkeit erzielen. Die international ausgerichtete Messe für Schleiftechnik GrindingHub bietet vom 17. bis zum 20. Mai in Stuttgart einen kompakten Marktüberblick für Produktionstechnologien in diesem anspruchsvollen Umfeld.
Hybride Maschinen für zahlreiche Fertigungslösungen
Große Stückzahlen, enormer Kostendruck und präzise Fertigungsabläufe zählen zu den hohen Hürden im Getriebebau. Und sie werden sogar noch weiter steigen, denn die Veränderungen in der Automobilindustrie betreffen gerade diesen Bereich besonders. Es gilt, künftig deutlich mehr Getriebevarianten herzustellen. Wie begegnen Firmen dieser Herausforderung? Eine eindrucksvolle Antwort gibt der Maschinenbauer Emag GmbH & Co. KG aus Salach mit einer neu entwickelten Baureihe. Deren große Stärke ist, dass sie dank der Kombination aus Schleifen und Drehen – plus weiterer Verfahren – inklusive Automation zahlreiche Fertigungslösungen gestattet. Die vollständige spanende Bearbeitung von Getriebebauteilen lässt sich damit abbilden.
Inzwischen hat das Unternehmen eine weitere Maschine im Portfolio: Sie ist zum einen größer und für Bauteile bis zu 350 mm Durchmesser ausgelegt. Zum anderen gibt es erstmalig die Option, eine Schleifspindel mit NC-Schwenkachse zu integrieren. Auf ihr befindet sich beispielsweise ein zylindrischer Schleifkörper, mit dem sich innenliegende Bohrungen schleifen lassen - vom Hartdrehen der Planflächen über das Vordrehen der Bohrung und des äußeren Synchronkegels bis hin zum Fertigschleifen dieser Konturen.
Verbesserte Oberflächentreue und Wirtschaftlichkeit
Der Vormarsch additiver Fertigungsverfahren scheint unaufhaltsam, denn sie überzeugen durch eine ganze Reihe von Vorteilen. Neben Produktivitätsgewinnen wie dem Verzicht auf klassischen Werkzeugbau und flexible Produktion erlaubt die große geometrische Gestaltungsvielfalt auch die Umsetzung komplexerer Bauteile. Allerdings bleibt eine Nachbearbeitung meist nicht aus. Je nach Bauteil und Prozess gilt es, mögliche Hilfs- und Stützstrukturen des additiven Verfahrens zu entfernen. Sonst müssen Oberflächenbearbeitungen wie Fräsen, Schleifen oder Superfinish und eine Bauteilkontrolle vorgenommen werden.
Für mehr Effizienz ist es allerdings notwendig, sowohl die additive als auch die subtraktive Fertigung als hybrides System zu erfassen. Schon beim Bestimmen des 3D-Modells müssen die Bedürfnisse der Nachbearbeitung einfließen. Im Idealfall findet eine direkte Datenintegration entlang der Prozesskette statt. In der Praxis heißt das: Die Prozesse sind präzise aufeinander abgestimmt und werden ohne weiteres Werkstückhandling durchgeführt. Robotergestützte und automatisierte Lösungen wie die innovative Fertigungszelle für automatisierte Oberflächenbearbeitungen der Supfina Grieshaber GmbH & Co. KG aus Wolfach setzen genau hier an. In nur einer Aufspannung lassen sich Prozesse flexibel kombinieren und nahtlos in die Produktion integrieren. Das führt sowohl zu einer hohen Oberflächentreue als auch zu verbesserter Wirtschaftlichkeit.
Hocheffiziente Werkzeugfertigung mittels Kombinationsbearbeitung
Die Entwicklung von immer komplexeren und präziser arbeitenden Werkzeugen aus unterschiedlichen Materialien stellt eine Herausforderung für die Herstellung von Werkzeugschleifmaschinen dar. „Nicht alle Materialien oder Kombinationen davon lassen sich durch Schleifen final bearbeiten“, weiß Siegfried Hegele, Produktmanager Applications bei der Walter Maschinenbau GmbH, Tübingen. „Hier sind auch Technologien wie das Erodieren oder Lasern gefordert, inklusive Messtechnik. Walter und Ewag bieten als System- und Lösungsanbieter die für jeden Werkzeugbearbeitungsfall passende Lösung aus einer Hand an."
Der Fertigungsprozess beispielsweise eines PKD (polykristallinen Diamant)-bestückten Fräswerkzeugs basiert auf mehreren Schritten. Hierbei wird ein gesintertes Hartmetallwerkzeug zunächst rundgeschliffen. Anschließend erfolgt das Schleifen der Spanräume. Um diese Arbeitsschritte effizient durchzuführen, ist eine Maschine mit hoher Spindelleistung notwendig. Der nächste Schritt umfasst das Schleifen von Plattensitzen in den Hartmetallkörpern. Bevor als Nächstes gelötet werden kann, ist zu kontrollieren, ob die Toleranzen bei den Schleifvorgängen eingehalten worden sind. Dies geschieht idealerweise auf einer automatischen CNC-Messmaschine. Als nächster Schritt sollten die vorab aus einem PKD-Rondell ausgeschnittenen PKD-Platten in die Plattensitze gelötet werden. Hierbei wird der polykristalline Diamant kurzzeitig bis annähernd auf Graphitisierungstemperatur erhitzt. Danach muss das Werkzeug gereinigt werden und es ist zu entscheiden, welche Technologie für das Bearbeiten des PKD infrage kommt. Hier kann eine Kombinationsbearbeitung mit verschiedenen Technologien, zum Beispiel Schleifen und Erodieren, deutliche Vorteile bringen. Abschließend erfolgt eine erneute Messung zur Qualitätskontrolle.
Zeiten verkürzen, Produktivität und Qualität verbessern
Auch die Kombination von Fertigungsprozessen eröffnet neue Potenziale in der Produktion. Die klassische Motivation zur hauptzeitparallelen Bearbeitung eines Werkstücks innerhalb einer Maschine, die beispielsweise über mehrere Spindeln verfügt, ist die Verringerung der Zykluszeit. Grundsätzlich sind die dafür erforderlichen Maschinen jedoch mit hohen Investitionskosten verbunden und aufgrund der geringen Flexibilität nur für große Stückzahlen wirtschaftlich. Des Weiteren kann die Hybridbearbeitung auf einer Maschine zur Steigerung von Qualität, Produktivität und Prozesssicherheit beitragen, da weniger Fehler durch das Spannen sowie den Transport von Bauteilen auftreten.
Neben einer Kombination aus Schleiftechnologie und trennenden Verfahren mit geometrisch bestimmter Schneide ist auch das Zusammenspiel unterschiedlicher Schleifverfahren innerhalb einer Maschine höchst sinnvoll. Bei Verzahnungen wird beispielsweise die Bearbeitung durch spezielle Finishingverfahren zunehmend innerhalb der Schleifmaschine durchgeführt. Für das Finishing sind bislang oft zusätzliche Anlagen etwa für das Gleitschleifen notwendig, die häufig nur bei externen Dienstleistern zur Verfügung stehen. „Bei der Herstellung von Verzahnungen in der Automobilindustrie fand in der Vergangenheit aus Kostengründen nur selten eine Nachbearbeitung statt. Hier kommen nun immer mehr hybride Werkzeugkonzepte zum Einsatz, mit denen sich sowohl die Schleif- als auch die Finishingbearbeitung durchführen lassen“, weiß Prof. Eckart Uhlmann, Leiter des Fraunhofer-Instituts für Produktionsanlagen und Konstruktionstechnik (IPK) in Berlin. Er ist zudem Mitglied in der WGP (Wissenschaftlichen Gesellschaft für Produktionstechnik), einem Zusammenschluss führender Professorinnen und Professoren der Branche. „Seit kurzem will auch die GrindingHub als Informationsdrehscheibe alle Möglichkeiten für den fundierten Wissensaustausch bieten.“
Als internationale Plattform bietet die GrindingHub 2022 sämtliche Prozesse für Schleiftechnik und Superfinishing ab. Der Veranstalter VDW schafft in Kooperation mit der Messe Stuttgart und Swissmem die dafür notwendige solide Basis. Schleifmaschinen, Werkzeugschleifmaschinen und Schleifmittel stehen hierbei im Fokus – flankiert von Softwarelösungen, Automationsangeboten und begleitenden Dienstleistungen.
Info zur GrindingHub HIER
Quelle: Verein Deutscher Werkzeugmaschinenfabriken e.V. (VDW) , Dag Heidecker (daxTR) / Vorschaubild: Supfina Grieshaber / Beitragsbild: EMAG