Optimierung von Instandhaltung und Asset Management hebt Einsparungspotenziale in der Stahlindustrie
von unsem Gastkommentator
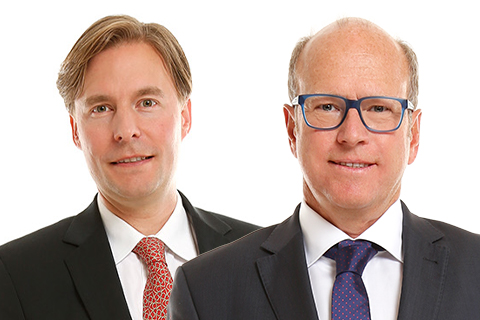
Die Stahlindustrie steht unter einem erheblichen Veränderungsdruck. Wichtigster Treiber ist dabei die Klimapolitik in Deutschland und der EU. Deutschland will seine CO2-Emissionen bis 2030 um 65 Prozent senken, Basisjahr ist 1990, und bis 2045 Netto-Null-Emissionen erreichen. Die EU setzt das Senkungsziel bei 55 Prozent und fordert die Klimaneutralität bis 2050. Für die Stahlindustrie in Deutschland, die mit rund 54,25 Millionen Tonnen CO2 etwa 30 Prozent der Emissionen der gesamten Industrie produzierte (Quelle: Wirtschaftsvereinigung Stahl, Fakten zur Stahlindustrie 2020), bedeuten diese Ziele Milliardeninvestitionen in neue oder modernisierte Anlagen. Vor diesem Hintergrund bekommt die Effizienz der Produktion für stahlproduzierende Unternehmen eine noch größere Bedeutung, um durch Einsparungen Mittel für Investitionen freizusetzen. Immer mehr Unternehmen erkennen daher die Bedeutung des Instandhaltungs- und Asset Managements, dessen Anteil an den Kosten der Stahlproduktion 54 bis 72 Prozent beträgt.
Stahlindustrie erst auf dem Weg zu proaktiver Instandhaltung
ConMoto hat mit dem MaintenanceScoreTest ein Verfahren zur objektiven Bewertung der Performance und des Reifegrades der Instandhaltung entwickelt und es in den vergangenen Jahren in mehr als 260 Produktionsstätten durchgeführt. Dieses fünftägige Testverfahren analysiert und bewertet Prozesse, Strukturen und Kennzahlen der Instandhaltung. Die Testergebnisse werden von einem interdisziplinären Team aus Management und operativen Mitarbeitern interaktiv erarbeitet und bieten eine ganzheitliche Sicht auf die Stärken und Schwächen. Das resultierende unternehmensspezifische Effizienz- und Reifegradprofil wird dann mit Best Practice verglichen.
Im Vergleich zu anderen anlagenintensiven Branchen ist der Reifegrad der Instandhaltung und des Asset Managements in der Stahlindustrie und in metallverarbeitenden Unternehmen noch nicht weit fortgeschritten, das hat die Analyse in 16 Betrieben ergeben. Die Branche befindet sich im unteren Reifegrad-Mittelfeld mit im Durchschnitt 5,0 von 12 möglichen Punkten und ist erst auf dem Weg dahin, alle Möglichkeiten eines proaktiven Instandhaltungsmanagements zu nutzen. Die Bewertung des Branchenbesten lautet 6,7. Wie viel finanzielles Einsparungspotenzial ungenutzt bleibt, wird deutlich, wenn man sich vor Augen führt, dass in der Stahlindustrie 18 Prozent der direkten Instandhaltungskosten und 36 bis 54 der indirekten Instandhaltungskosten in Form von Produktionsausfallkosten von der Qualität der Instandhaltung abhängen.
Gezielte Maßnahmen zur Verbesserung der OEE und zur EBIT-Steigerung
ConMoto hat in 16 Betrieben der Stahlindustrie und der metallverarbeitenden Industrie den Reifegrad analysiert und die Optimierungspotenziale in der Instandhaltung ermittelt und gehoben. Die Ergebnisse verdeutlichen nochmals wie groß die Verbesserungsmöglichkeiten sind:
- Reduzierung der Instandhaltungskosten um 5 bis 20 %
- Reduzierung der Fehlerraten um 30 bis 70 %
- Senkung der Ersatzteilbestände um 15 bis 30 %
- Steigerung der Overall Equipment Effectiveness (OEE) um 5 bis 14 %
- Positiver EBIT-Effekt 10 bis 48 %
Die Gestaltungsfelder in der Instandhaltung, um diese Effekte in der Branche zu realisieren, sind vielfältig. Zu den Kernstellgrößen gehören:
- Risiko- und verfügbarkeitsorientierte Instandhaltungsstrategie auf Komponentenebene,
- Instandhaltungsauftragsmanagement mit Kapazitäts- und Terminplanung,
- In- und Outsourcing von Leistungen,
- Ersatzteilmanagement,
- Anlagenbediener-Autonome Instandhaltung,
- Kennzahlen und Visualisierung,
- Shutdown Management.
Optimales Anlagenmanagement über die gesamte Lebensdauer
Auf dem Weg zu Best Practice wird "Instandsetzung" durch ein ganzheitliches Asset Management abgelöst. Dabei gilt es, in einem ersten Schritt mehr aus den vorhandenen Anlagenkapazitäten herauszuholen und gleichzeitig die Gesamtkosten zu minimieren. In einem zweiten Schritt wird darauf aufbauend ein zukunftsfähiges Asset Management mit der notwendigen Innovationskraft implementiert. Asset Innovation kombiniert dabei lebensdaueroptimiertes Anlagenmanagement mit innovativer Anlagenplanung. Insbesondere in anlagenintensiven Betrieben der Stahlindustrie, Metallherstellung und -verarbeitung ist dies der Schlüssel für eine gezielte Steigerung der Unternehmenswertschöpfung und die nachhaltige Sicherung der Wettbewerbsfähigkeit.
ConMoto nutzt seine Erfahrung aus Projekten in unterschiedlichen Branchen und integriert Asset Innovation bereits in die Anlagenplanung, um die Lebenszykluskosten um 20 bis 30 Prozent zu reduzieren. Dadurch können je nach Lebensdauer der Anlagen Lebenszykluskosten in Höhe des ein- bis dreifachen des anfänglichen Investitionsvolumens eingespart werden. Die Anlagengesamtkosten können in Abhängigkeit von der Anlagenlebensdauer bis zum Fünffachen der ursprünglichen Anschaffungskosten betragen. Gerade bei kapitalintensiven, langlebigen Produktionsanlagen ist deshalb ein kontinuierliches und wertorientiertes Asset Management unabdingbar. Es sichert das produktive Optimum der Anlage über ihren gesamten Lebenszyklus und damit das wirtschaftliche Optimum der Investitionen. ConMoto implementiert die Best-Practice-Gestaltungselemente für Hochleistungsproduktionsanlagen und Asset Innovation, um diese Potenziale zu heben.
Dies ist insbesondere vor dem Hintergrund der zukünftigen Investitionen zum Green-Steel elementar wichtig. Jetzt ist der richtige Zeitpunkt, ein modernes innovatives Instandhaltungsmanagement für die Stahlproduktion der Zukunft aufzubauen.
Auf dem Bild links: Dr. Marc A. Heinisch, ConMoto Partner und CSO
Auf dem Bild rechts: Dipl.-Ing., MBA Nils Blechschmidt ConMoto Partner / Head of Maintenance/Asset Management & Process Industry
Foto: ConMoto