In der Messtechnik geht der Trend in Richtung Vollautomatisierung
von Dagmar Dieterle
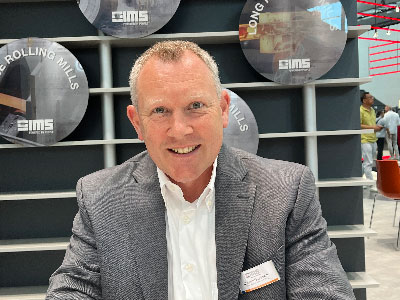
Die IMS Messsysteme GmbH in Heiligenhaus ist auf die Fertigungsprozessgestaltung in der Stahl-, Buntmetall- und Aluminiumindustrie spezialisiert, wobei Produktivität, Flexibilität, Material- und Energieeffizienz sowie Wirtschaftlichkeit im Fokus stehen. IMS entwickelt und vertreibt hochpräzise Messtechnik, um den steigenden Qualitätsanforderungen an Stahl-, Aluminium- und Buntmetallerzeugnisse gerecht zu werden. Die Präzisionsmesssysteme sind digital, vernetzt und automatisiert und können an individuelle Prozessabläufe angepasst werden.
Wir sprachen mit Herrn Dipl.-Ing Christian Knackstedt, Division Manager Sales and Marketing der IMS Messsysteme GmbH
marketSTEEL: Die Anforderungen an die Oberflächengüte von gewalzten Bändern, Blechen und Platten steigen stetig. Weiterverarbeitenden Industrien fordern heute Ausgangsmaterialien mit makellosen, ebenen Oberflächen.
Es wird immer wichtiger, dass Oberflächen frei von Fehlern sind - besonders im Automobilbereich, wo qualitativ hochwertige Oberflächen benötigt werden. Dazu ist es notwendig, Oberflächendefekte unter Produktionsbedingungen sicher zu erkennen und korrekt zu klassifizieren. Darüber hinaus wird es immer wichtiger, auf Basis der erkannten Defekte die Produktqualität zu bewerten, um vollautomatisch zu entscheiden, ob das Produkt den gewünschten Kundenanforderungen genügt oder eine Nachbearbeitung notwendig wird.
marketSTEEL: Wie funktioniert die zuverlässige Beurteilung von Oberflächenfehlern?
Grundlage einer zuverlässigen Fehlererkennung ist erst einmal eine optimale Bildaufnahme, zu der je nach Anforderung verschiedene Kamera- und Beleuchtungsgeometrien miteinander kombiniert werden können. In der Regel sind das schnelle Zeilensensoren und LED-Beleuchtungen, aber auch Lasertriangulationssysteme werden immer leistungsfähiger und sind insbesondere in den Anwendungen interessant, in denen die Tiefe von Defekten ein Qualitätskriterium darstellt.
Auf diesen Bildern werden mit Hilfe von Detektions- und Segmentierungsalgorithmen die Fehlstellen bestimmt, zu denen der Klassifikator eine Klassifikationsaussage trifft. Weitere kundenspezifische Regelsets erlauben in der Nachbearbeitung dann eine Adaption an die konkreten Qualitätsanforderung des Produkts, beispielsweise anhand von Werksnormen.
marketSTEEL: Setzen Sie dafür KI ein?
Künstliche Intelligenz ist ein zentraler Baustein unserer Oberflächeninspektionssysteme und liefert bei der Klassifikation der Defekte einen wichtigen Beitrag. Wir setzten dabei hauptsächlich Methoden des überwachten Lernens ein, indem ein Klassifikator auf einer Trainingsdatenbank trainiert wird. Hier kann auf vortrainierte Modelle zurückgegriffen werden, die dann in einer Optimierungsphase kundenspezifisch angepasst werden können.
Wir arbeiten kontinuierlich daran, diesen komplexen Prozess für unsere Kunden intuitiv zu gestalten. Aus diesem Grund beteiligen wir uns aktiv als Pilotpartner am Forschungsprojekt Humaine der Metropole Ruhr zum Thema humanzentrierter Arbeit mit KI.
marketSTEEL: Messaufgaben werden immer komplexer. Können Sie uns einige Beispiele nennen?
Natürlich. Als einen der ersten Schritte in der Produktionskette werden zum Beispiel immer höhere Anforderungen an die Dickenmessung oder Dickenprofilmessung gestellt, um den stetig steigenden Ansprüchen der Hersteller und deren Kunden gerecht zu werden. Darüber hinaus gibt es natürlich auch – um bei dem Beispiel zu bleiben – stetig steigende Anforderungen im Hinblick auf die Präzision von Oberflächeninspektionssystemen. Insgesamt fordert die Industrie für immer mehr anfallende Messaufgabe in der Produktion, angefangen beim Stranggießen, bis hin zu Metal Service Centern, Präszionsmesssysteme mit einer hohen Reproduzierbarkeit.
marketSTEEL: Kostenfaktor: Je besser die Oberflächen, umso geringer der Ausschuss?
Generell gilt nicht nur für die Qualität der Oberfläche, dass Mehraufwände deutlich reduziert werden können, je früher im Prozess Fehlstellen detektiert und Ursachen von Qualitätsabweichungen behoben werden. Wir haben ein neues Produkt namens IDS (Magnetbasiertes Inclusion Detection System für Bandstahl), das gerade als Messeschwerpunkt präsentiert wird. Mit diesem Inclusion Detection System können innere Einschlüsse im Material aufgespürt werden, ebenso wie Schalendefekte und optisch nicht detektierbare Oberflächenfehler. Drei Faktoren, die bei rechtzeitiger Erkennung die Ausschussquote deutlich senken kann. Dieses System ist besonders interessant für Stahlhersteller, da das zu prüfende Messgut magnetisierbar sein muss. Die Stahlbranche steht zunehmend unter Druck, fehlerfreies Material zu liefern. Als Lieferant von Messsystemen ist es unsere Herausforderung, für die relevanten Messaufgaben Systeme zu entwickeln und auf den Markt zu bringen. Viele unserer Messsysteme sind übrigens auf konkrete Anfragen von Kunden hin entwickelt worden und bedienen daher die Anforderungen der Branche.
marketSTEEL: Wie sind Ihre Visionen? Wohin geht der Trend bei Messystemen?
Der Trend geht eindeutig in Richtung vollautomatisierter Messungen. Angefangen bei der Flüssigphase und dem Stranggießen über das klassische Warmwalzen bis hin zum Kaltwalzen wird das Material durchgängig auf Toleranzabweichungen und Fehler untersucht und überprüft.
Das Ziel ist es, schnell in den laufenden Prozess eingreifen und unmittelbar nachjustieren zu können, sobald es Abweichungen gibt und die gestellten Anforderungen nicht erfüllt sind. Dadurch wird kein – fehlerhaftes – Coil fertig produziert, sondern nachbearbeitet, bevor es in den weiteren Produktionsprozess einläuft.
Diese Vision beinhaltet entsprechend die Vollautomatisierung von Messungen aller Größen des Materials oder aller qualitätsrelevanten Eigenschaften vom Beginn des Produktionsprozesses bis zum fertigen Coil.
marketSTEEL: Danke für das Gespräch.
Fotos: marketSTEEL