E-Auto-Rotorwellen im schnellen Takt hochgenau verzahnen
von Angelika Albrecht
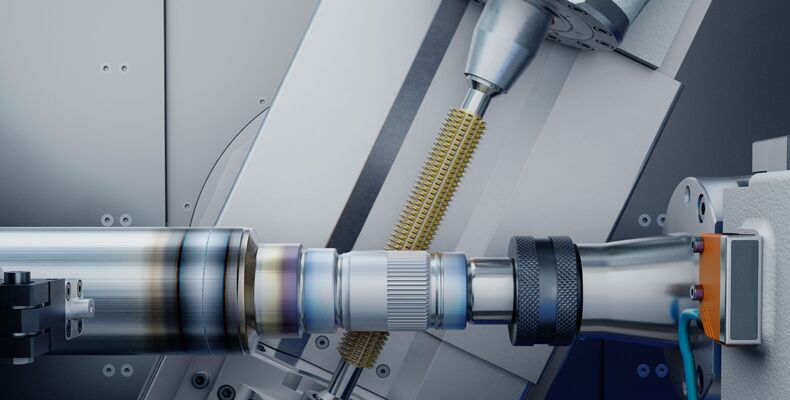
Es ist eine anspruchsvolle Bearbeitungsaufgabe, die Verzahnung einer Rotorwelle für E-Autos zu bearbeiten: In kaum einem anderen Anwendungsfeld werden an Getriebekomponenten so hohe Anforderungen gestellt. Dabei geht es um höchste Oberflächengüten, damit keine störenden Laufgeräusche im sehr leisen Motor auftreten. Zudem steigen aktuell die Stückzahlen in der E-Mobilität massiv an, was den beteiligten Maschinenbau zusätzlich herausfordert. Gesucht werden also prozesssichere Lösungen für eine kostengünstige Rotorwellen-Produktion. Wie das funktionieren kann, demonstriert aktuell EMAG Koepfer: Die Wälzfräsmaschine HLC 150 H sorgt für eine neue Produktivität in diesem Verzahnungsbereich.
Dass E-Autos keinerlei Getriebe (abseits des teilweise unverzichtbaren Differentials) aufweisen, ist nur eine Legende – die sich allerdings recht hartnäckig in der Öffentlichkeit hält. Sie beruht auf der Annahme, dass der E-Motor angesichts seines stabilen Drehmoments keinerlei Übersetzung benötigt. Tatsächlich ist es in der Praxis aber zumeist so, dass ein sogenanntes 1-Gang-Getriebe zum Einsatz kommt, mit dessen Hilfe die Drehzahl des E-Motors um einen bestimmten Faktor reduziert wird. In der Folge gibt es zahlreiche Verzahnungselemente an Bauteilen wie Antriebswelle, Rotorwelle oder Achsantrieb, wobei ihre Bauteilqualität außergewöhnlich sein muss, damit zum Beispiel keine lauten Laufgeräusche entstehen – angesichts des leisen E-Motors wären diese zu hören.
Hohe Verzahnungsqualität punktet
Die Spezialisten von EMAG Koepfer entwickeln seit vielen Jahren sehr vielseitige Maschinenbau-Lösungen für die Bearbeitung eines riesigen Werkstückspektrums von Getriebewellen über Lenkritzel und Schneckenräder bis zu Planetenrädern – eine ideale Erfahrungsbasis, um auch für die Verzahnung von Rotorwellen hocheffiziente Lösungen bereitzustellen. Die Wälzfräsmaschine HLC 150 H bietet ein hohes Maß an Produktivität bei Bauteilen mit einer maximalen Länge von 500 Millimetern und einem Gewicht von 10 Kilogramm. Dafür sorgt zunächst einmal der Fräskopf. Er ist sehr steif aufgehängt und verfährt während der Bearbeitung komplett. Die Shift-Achse setzt sich aus der Interpolation zweier Achsen zusammen. So wird ein großer Fräskopf-Schwenkwinkel bei gleichzeitig großem Shift-Weg realisiert. Deshalb vollzieht sich das Wälzfräsen sehr ruhig und die Verzahnungsqualität ist hoch. Durch die horizontale Anordnung des Werkstücks entstehen zudem keine Spänenester. Im Endergebnis sorgt diese Technologie für enorme Leistungskennzahlen bei der Bearbeitung von Rotorwellen mit Taktzeiten von nur 35 Sekunden bei einer Verzahnungsqualität von DIN Q7.
In die Linie integrierbar
EMAG plant und entwickelt komplette Linien für die Rotorwelle, in denen alle Bearbeitungsprozesse perfekt verkettet hintereinander ablaufen – von der Weichbearbeitung der Rohlinge bis zur abschließenden Hartbearbeitung inklusive der Zahnflanken-Schleifprozesse oder des Schälwälzfräsens. Auch die HLC 150 H kommt hierbei zum Einsatz, was angesichts ihres integrierten Hochgeschwindigkeits-Ladeportals kein Problem darstellt. Es entnimmt die Bauteile vom EMAG eigenen TrackMotion-System, das gewissermaßen durch die Maschinen der Linie hindurchfährt.
Im Übrigen verfügt EMAG Koepfer über die Wälzfräsmaschine K 160 – eine Lösung für Bauteile mit einer maximalen Länge von 300 Millimetern und einem Gewicht von 2,5 Kilogramm, was vor allem für gebaute Rotorwellen interessant ist, denn ihre Einzelteile sind (vor dem Fügen) verhältnismäßig klein und leicht.
Insgesamt sieht sich EMAG Koepfer gut gerüstet für den anwachsenden E-Auto-Boom. Wenn es darum geht, in diesem Bereich eine großvolumige Produktion aufzubauen, bieten die Verzahnungsexperten hocheffiziente Lösungen, die sich in ganz unterschiedlicher Weise in den Herstellungsfluss integrieren lassen.
Quelle und Vorschaubild: EMAG GmbH & Co.KG