Additive Fertigung ist Zukunftsthema der Produktionstechnik
von Alfons Woelfing
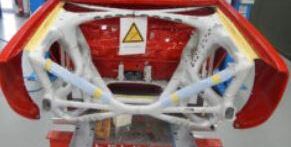
Additive Fertigung ist das große Zukunftsthema der Produktionstechnik. Der dreidimensionale Druck ergänzt immer stärker herkömmliche Fertigungstechniken und ist in vielen anspruchsvollen Industrien wie der Medizintechnik, der Automobilindustrie und der Luft- und Raumfahrt bereits erfolgreich im Einsatz. Auch Gießereiindustrie, Stahl- und Aluminiumbranche haben das Potenzial des 3D-Drucks erkannt. Das Düsseldorfer Messequartett GIFA, METEC, THERMPROCESS, NEWCAST 2019 (25. bis 29.Juni 2019) widmet dem Thema „Additive Manufacturing“ aus diesem Grund eine eigene Sonderschau.
Ein Blick unter die Motorhaube des Demonstratorfahrzeugs zeigt das Potenzial des industriellen 3D-Drucks für die Automobilindustrie: Wenige Bauteile, dafür mit Funktionserweiterungen und einer erheblichen Gewichtseinsparung. Die 34 kg leichte crashsichere neue Vorderwagen-struktur des alten VW Caddys ist aus der hochfesten und hochzähen Hochleistungslegierung Scalmalloy der Airbus-Tochter APWorks mit einem 3D-Drucker der deutschen EOS gefertigt. Das unter Federführung des Entwicklungsdienstleisters csi laufende Projekt 3iprint wurde Mitte Juni mit dem „German Innovation Award 2018“ ausgezeichnet. Das Caddy-Konzept soll aufzeigen, was unter Anwendung neuer Konstruktionsmethoden und neuer Werkstoffe mit additiver Fertigung im Automobilbau technologisch möglich ist.
Generativen Fertigungsverfahren, wie der Oberbegriff für die unterschiedlichen additiven Fertigungstechnologien mit allen möglichen Typen von 3D-Drucksystemen lautet, gehört die Zukunft. Schon heute ist die additive Fertigung mit Kunststoffen, Metallen und Keramik aus der Industrie nicht mehr wegzudenken. Knapp 40 Prozent der 2016 befrag-ten deutschen Unternehmen nutzten 3D-Druck bereits, wie die Beratungsgesellschaft EY ermittelt hat. Das Potenzial quer durch alle Bereiche ist gewaltig. 3D-Druck mit Beton könnte die Baubranche revolutionieren, Bioprinting von lebendem Gewebe ist bereits möglich – und selbst der Druck menschlicher Organe ist ein ernsthaft verfolgter Forschungsgegenstand.
Den Metallbranchen – ob Gießerei oder Stahlerzeuger, Schmiede oder Blechverarbeiter – bietet der 3D-Druck neue Chancen. Mit dem 3D-Drucker erfolgt der Aufbau Schicht für Schicht auf Basis digitaler Kon-struktionsdaten. Material wird nur an den Stellen verbaut, wo es gebraucht wird. Wo konventionelle Fertigungsverfahren wie Gießen, Fräsen oder Schmieden an ihre Grenzen stoßen, spielen additive Technologien ihre Stärken aus. 3D-Druck bietet Konstrukteuren uneingeschränkte geometrische Freiheiten. Mit variierenden Wandstärken, Hohlräumen und Wabenstrukturen lassen sich beispielsweise komplexe funktionsintegrierte Bauteile mit bionischem Aufbau fertigen, wie eben die hochbelastbare automobile Leichtmetallkonstruktion aus dem 3iprint-Projekt.
Im dreidimensionalen Druck ist auch eine Fertigung kleiner Losgrößen und selbst von Einzelstücken wirtschaftlich darstellbar. Druckgießwerkzeuge oder Umformwerkzeuge entfallen, was schnell mehrere zehntausend Euro an Werkzeugkosten einsparen kann. Individualisierte Bauteile, Prototypen und selten nachgefragte Ersatzteile gelten daher als Domänen der additiven Fertigung.
Die universale Angriffswaffe zum Sturm auf die Bastionen der etablierten Fertigungswelt ist der 3D-Druck indes nicht. „Additive Fertigung“, sagt der Fertigungsexperte Franz-Josef Wöstmann vom Fraunhofer Institut IFAM in Bremen, „ist Ergänzung, nicht Substitution.“ 3D-Drucker geraten spätestens dort an ihre Grenzen, wo sich mit konventionellen Fertigungsverfahren hohe Stückzahlen wirtschaftlich erzielen lassen. Das fällt insbesondere bei metallischen Fertigungsverfahren im Großvolumensegment der Automobilindustrie ins Gewicht.
Die Produktivität additiver Fertigung mit Metall ist gegenwärtig wenig großserientauglich. „3D-Druck wird für Premiumfahrzeuge und für eine beschränkte Anzahl an Bauteilen mehr und mehr kommen, die Gießerei aber nicht ersetzen können“, ist sich Dr. Stefan Geisler, Innovationsmanager der KSM Casting Group in Hildesheim, sicher. Die im Volumenmarkt benötigten Stückzahlen würden sich auch mit schnelleren Aufbauraten wie bei additiver Fertigung mit Draht nicht erreichen lassen. „Was gern vergessen wird, ist, dass auch die additive Fertigung die Physik nicht überlisten kann. Auch da geht es am Ende nur um Prozesse: Aufschmelzen und Abkühlen. Das geht nicht beliebig schnell“, gibt Geisler zu bedenken. Zudem müssen die gedruckten Komponenten durch spanende Prozesse zum fertigen Funktionsbauteil veredelt werden.
Nachteilig bei metallischer additiver Fertigung ist in jedem Fall auch der hohe Energieaufwand. Beim Laserschmelzen von Metall muss von der Pulverherstellung bis zum fertigen Bauteil rund zweimal so viel Energie aufgewendet werden wie beim konventionellen Gießen, wie der Münchner Professor Wolfram Volk, Ordinarius des Lehrstuhls für Umformtechnik und Gießereiwesen der TU München, vorrechnet.
Additive Verfahren werden zunehmend zum Bestandteil bestehender Prozessketten. Wie sich additive und zerspanende Bearbeitung in einem Bearbeitungszentrum zu hybrider Komplettbearbeitung kombinieren lässt, zeigen u.a. die Werkzeugmaschinenhersteller DMG Mori und Hermle. Weltmarktführer DMG Mori ergänzt das Laserauftragsschweißen mittels Pulverdüse (Laser Metal Deposition) um die zerspanende Nachbearbeitung mit Drehen und Fräsen. Wettbewerber Hermle erweitert mit seiner MPA-Technologie (Metall-Pulver-Auftrag) ein mehrachsiges Bearbeitungszentrum um ein thermisches Spritzverfahren, bei dem Metallpulver schichtweise zu einem soliden Bauteil verfestigt wird.
Höhere Aufbauraten bei der additiven Verarbeitung von Metallen verfolgt das Berliner Unternehmen Gefertec. Die 5-Achsen-Anlagen der Maschinenbauer für generative Fertigungstechnik schweißen Draht im Lichtbogenverfahren Lage für Lage aufeinander. Die so gefertigten Rohlinge kommen der Endkontur sehr nahe, was den Zeit- und Werkzeugeinsatz der spanenden Nachbearbeitung reduziert.
Gießerei: Direkte und indirekte Verfahren additiver Fertigung
Von generativen Verfahren gleich mehrfach profitieren kann die Gießereiindustrie. Direkte Verfahren der additiven Fertigung bieten Gießereien die Chance, auch Teile geringer Stückzahl bis hin zu Unikaten ins Produktportfolio aufzunehmen. Im indirekten Verfahren wiederum nutzen sie additive Technologien zur Herstellung von Formen und Kernen aus Sand und von Modellen aus Kunststoff. Weiteres Potenzial bieten Hybridtechnologien mit einer Verfahrenskombination aus konventionellem Gießen und additiver Fertigung.
Unter den Systemherstellern für additive Fertigung nimmt die deutsche Industrie eine Spitzenposition ein, wie der BDI in einem Positionspapier festhält. Bei den Pulverbettsystemen liegt ihr Marktanteil bei rund 70 Prozent. Zu den global führenden 3D-Druckerherstellern zählen EOS (Metall und Kunststoff), SLM Solution (Metall) und Voxeljet. Voxeljet hat sich auf Gießereien spezialisiert und vertreibt 3D-Drucker zur Herstellung von Sandformen und Kernen, sowie von Kunststoffmodellen für den Feinguss nach dem Ausschmelzverfahren.
Um ein Gussteil zu gießen, braucht es eine Form, zur Ausbildung der Hohlräume in dem zu gießenden Teils die entsprechenden Kerne. Im klassischen Sandguss bestehen Formen und Kerne aus Quarzsand, der mit einem speziellen Bindemittel verfestigt wird. Während in der Großse-rienfertigung etwa von PKW-Motoren vollautomatische Formanlagen und sogenannte Kernschießautomaten zur Standardausrüstung moder-ner Gießereien gehören, ist bei Prototypen und kleineren Serien der Einsatz der Automaten selten wirtschaftlich. Hier kommt immer stärker der 3D-Druck zum Zug. Aus dem CAD-Datensatz heraus werden Sandformen und Kerne beliebiger Komplexität über einen Schichtbauprozess hergestellt. Diese werkzeuglose Fertigung bietet hohe Flexibilität bezüglich Stückzahl, Design und Varianten und erlaubt die Fertigung komplexer Formen und Kerne mit nahezu beliebiger Geometrie in exakt repro-duzierbarer Qualität. Voxeljet spricht beim 3D-Druck von Formen und Kernen aus Sand für Kleinserien über Kosteneinsparungen von bis zu 75 Prozent.
Das Drucken von Sandformen und -Kernen eignet sich optimal als Entwicklungsinstrument. Die Eisen-Gießerei Düker mit den Standorten Karlstadt und Laufach beispielsweise setzt im Bereich Kundenguss keine Modelle mehr ein. Zur Herstellung der additiv gefertigten Sandformen dient allein der CAD-Datensatz. Neue Produkte werden so in kurzer Zeit aus dem Rechner in Guss realisierbar und können zur Erprobung weiterbearbeitet werden. Geometrische Anpassungen sind einfach umzusetzen, nach Änderung der Konstruktionsdaten und dem Druck einer weiteren Form kann der erneute Abguss erfolgen. Die Entwicklungszeit wird durch dieses Verfahren signifikant verkürzt, wie Düker berichtet. So sei es gängige Praxis, Erstmuster innerhalb weniger Wochen herzustellen, für die im Serienprozess Monate verstreichen.
Auch der Druckguss mit Dauerformen aus Werkzeugstahl profitiert vom 3D-Druck. „Additive Fertigung bietet Druckgießern große Chancen“, wie Dr.-Ing. Ioannis Ioannidis, Chef des Druckgießmaschinenherstellers Oskar Frech und sowohl Vorstandsvorsitzender im Fachverband Gießereimaschinen als auch Vorstandsmitglied der Arbeitsgemeinschaft Additive Manufacturing im VDMA, im Interview mit der Zeitschrift Giesserei hervorhebt. Im 3D-Druck fertigt Frech beispielsweise eine komplexe Schlüsselkomponente für seine angussarme, Kreislaufmaterial (z.B. Aluminium oder Magnesium) sparende Werkzeugtechnologie FGS.
Die Form nimmt im Druckgießprozess eine Schlüsselstellung ein. Gefordert wird eine möglichst schnelle Erstarrung der Gussteile. Durch schnellere Abkühlung lässt sich die Prozesszeit eines Bauteils verkürzen, wobei gleichzeitig auch die Gussqualität verbessert wird. Das setzt eine ausreichende Wärmeabfuhr in der Gießform voraus, die klassischerweise durch Kühlbohrungen vorgenommen wird. Kühlbohrungen möglichst dicht an der formgebenden Oberfläche anzubringen sind allerdings verfahrensbedingt Grenzen gesetzt. Hier kann additive Fertigung Abhilfe schaffen, denn dank der großen Gestaltungsfreiheit lässt sich eine konturnahe Kühlung auch an kritischen Bereichen in der Form erzeugen.
Stahlbranche: Vielfache Chancen mit 3D-Druck
Nicht viel anders als beim Druckgießen verhält es sich bei der Warmumformung von Stahlblechen. Auch hier sorgt eine konturnahe Kühlung für eine Produktivitätssteigerung bei höherer Qualität. Im Werkzeugbau deutscher Autohersteller zählt additive Fertigung daher längst zu den Standardverfahren.
Stahlunternehmen entdecken additive Fertigung zunehmend als zusätzliches Geschäftsfeld. So hat sich der österreichische Technologie- und Stahlkonzern voestalpine vor zwei Jahren Düsseldorf zum konzernweiten Kompetenzzentrum für Metal Additive Manufacturing auserkoren. Erste Ergebnisse liegen vor. Zusammen mit dem Entwicklungsdienstleister Edag und dem Spezialisten für Simulationssoftware Simufact haben die Österreicher ein additiv gefertigtes Leichtbau-Haubenscharnier mit integriertem Fußgängerschutz entwickelt.
Rosswag aus Pfinztal bei Karlsruhe, die größte Freiformschmiede im süddeutschen Raum, führt mit additiver Fertigung vor, wie sich das beste zweier Welten verbinden lässt. Mit einer Kombination der beiden Fertigungsverfahren Schmieden und Selektives Laserschmelzen von Stahlpulver entstehen bei dem Traditionsunternehmen neue Produkte. Massive und materialreiche Bauteilbereiche werden konturnah durch Freiformschmieden hergestellt. Auf ein hochbelastbares, faserverlaufgerecht geschmiedete Rohteil wird anschließend mit dem 3D-Drucker additiv aufgebaut, um die komplexen Strukturen zu ergänzen. So wurden etwa bei einem Impeller mit additiv gefertigten Schaufelstrukturen Kanäle zur Strömungsbeeinflussung eingebracht.
Stahlanlagenbauer: Signifikante Gewichtsreduktion für dynamisch bewegte Bauteile
Jüngstes Mitglied im Club der additiven Fertigung ist der Spezialist für metallurgischen Maschinen- und Anlagenbau SMS group. Am Standort Mönchengladbach hat der führende Hersteller von Hütten- und Walzwerkstechnik eine neue Pilotanlage zur Metallpulverherstellung errichtet. Mit der Pulververdüsungsanlage verfolgt das Unternehmen mehrere Ziele. Zum einen will SMS sowohl im Kundenauftrag hochreines Metall-pulver für additive Fertigung herstellen als auch neue Werkstoffe entwickeln und erproben. Das Unternehmen kann dabei auf eine jahrzehntelange Erfahrung im Verdüsen von Eisenpulver beispielsweise zum Sintern zurückgreifen. Auch das umfangreiche metallurgische Know-how der Gruppe und die breite Kompetenz in thermischer Prozesstechnik bilden ein gutes Startkapital. Zum anderen möchte der Anlagenbauer mit dem Vertrieb von Pulververdüsungsanlagen den schnell wachsenden Markt der Metallwerkstoffe für additive Fertigungsverfahren bedienen.
Nicht zuletzt ist die eigene Metallpulverherstellung ein Glied in der eigenen Prozesskette für additive Fertigung. Mit der Herstellung von additiv gefertigten Sprühköpfen für Gesenkschmiedepressen hat der Anlagenbauer bereits erstes Potenzial der zukunftsweisenden Technologie für sich erschlossen. Sprühköpfe entfernen Zunder von Gesenken, kühlen die Oberfläche, bringen Schmierstoffe auf und trocknen die Gesenke. Der ursprüngliche Sprühkopf war ein massives und schweres Teil. Im dreidimensionalen Druck lassen sich sehr leichte und platzsparende Sprühköpfe fertigen, die individuell an die Gegebenheiten einzelner Gesenke angepasst sind. Wie das Unternehmen berichtet, führt der Einsatz der je nach Kundenwunsch wahlweise in Kunststoff oder Metall gefertigten 3D-Sprühköpfe zu einer Senkung der Taktzeit und einer Verlängerung der Werkzeug-Standzeit beim Gesenkschmieden.
Die Ergebnisse weiterer Projekte seien nicht weniger vielversprechend, wie SMS mitteilt. Ein neues Walzenkühlrohr für Drahtwalzwerke etwa überzeugt durch ein konturangepasstes Design mit integrierten Düsen. Durch den Einsatz von Alumide, einer Werkstoffkombination von Aluminium- und Kunststoffpulver, ist die Konstruktion leichter und kostengünstiger als das herkömmliche Bauteil. Im Bereich Stahl-Konverter konnten die für die Stahlschmelzen eingesetzten SIS-Injektoren um 60 Prozent verkleinert und aus einem einzigen anstatt aus acht Teilen hergestellt werden. Und Rohrschweißanlagen der SMS group können dank ge-druckter Teile zukünftig auch 14 Zoll und kleinere Rohrdurchmesser herstellen, da in einer hybriden Bauweise aus additiver und konventioneller Fertigung kleinere, aber leistungsstarke Schmierringe für die Expanderwerkzeuge machbar sind.
Sonderschau Additive Fertigung auf der GMTN 2019
Mit einer Sonderschau zu Additiver Fertigung erweitert die Messe Düsseldorf die Metallurgiemessen GIFA, METEC, THERMPROCESS und NEWCAST vom 25. bis 29.Juni 2019. Auf dem GIFA-Gelände zeigen Aussteller aus aller Welt neue Entwicklungen zu Additive Verfahren. Softwareunternehmen mit Lösungen von der 3D-Visualisierung und -Modellierung bis zur Datenaufbereitung sind ebenso vertreten, wie Anbieter von Metallpulvern und Herstellern von Maschinen, Anlagen und Verfahren für additive Fertigung und Nachbearbeitung.
Quelle und Foto: Messe Düsseldorf GmbH